Good day,
I am a junior aeronautical design engineer working on an oleopneumatic shock absorber for aircraft landing gear. I've attached a simple diagram (omits a lot of detail so that only what I am referring to is shown) to the post to show the layout of the problem. The shock absorber consists of a cylinder, a piston, and a floating piston (all the other parts, like valves etc. are ignored here). A gas spring at the top - a chamber of highly pressurized nitrogen gas - is separated from light mineral oil by the floating separator piston. The gas spring has a maximum operating pressure (absolute) of 80 bar at its ultimate. The floating piston slides along a rod in the middle. The oil at the bottom provides damping by flowing through a stationary orifice not shown on the diagram.
Selecting a piston seal and guide rings for the piston (below the oil) is straightforward. However, I would appreciate some advice for selecting the piston and rod seals on the floating piston, which separates the oil from the gas. Is it appropriate to choose hydraulic piston and rod seals (rated to 80 bar), as if it were a hydraulic cylinder? For rod seals, would it be appropriate to select two single-acting hydraulic rod seals that are aligned in opposite directions to seal in both directions (also rated to 80 bar)? Would it be good design/maintenance practice, during assembly, to apply a thin film of the oil above the floating piston (in the gas spring area) to lubricate the seals properly?
Any advice is appreciated. Thanks.
I am a junior aeronautical design engineer working on an oleopneumatic shock absorber for aircraft landing gear. I've attached a simple diagram (omits a lot of detail so that only what I am referring to is shown) to the post to show the layout of the problem. The shock absorber consists of a cylinder, a piston, and a floating piston (all the other parts, like valves etc. are ignored here). A gas spring at the top - a chamber of highly pressurized nitrogen gas - is separated from light mineral oil by the floating separator piston. The gas spring has a maximum operating pressure (absolute) of 80 bar at its ultimate. The floating piston slides along a rod in the middle. The oil at the bottom provides damping by flowing through a stationary orifice not shown on the diagram.
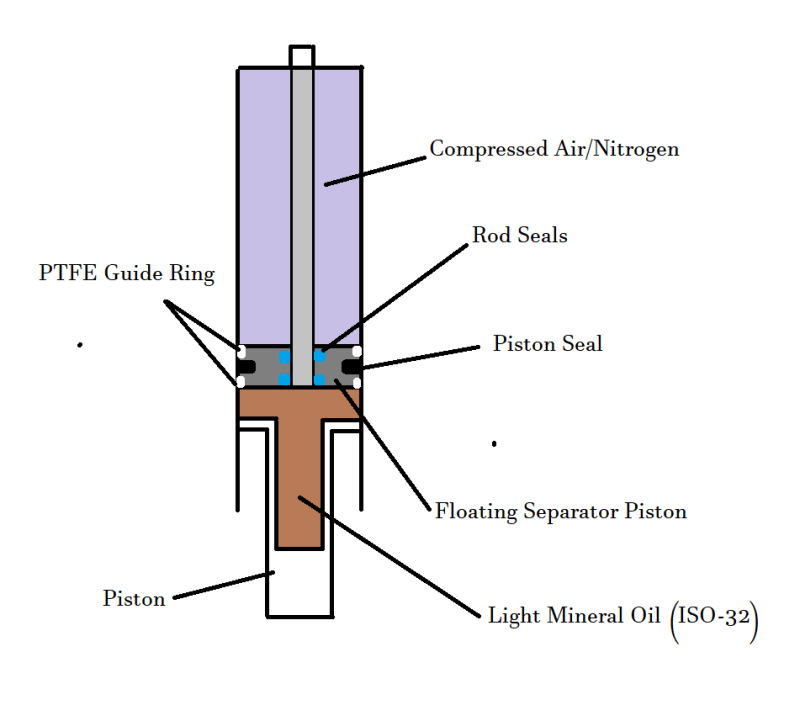
Selecting a piston seal and guide rings for the piston (below the oil) is straightforward. However, I would appreciate some advice for selecting the piston and rod seals on the floating piston, which separates the oil from the gas. Is it appropriate to choose hydraulic piston and rod seals (rated to 80 bar), as if it were a hydraulic cylinder? For rod seals, would it be appropriate to select two single-acting hydraulic rod seals that are aligned in opposite directions to seal in both directions (also rated to 80 bar)? Would it be good design/maintenance practice, during assembly, to apply a thin film of the oil above the floating piston (in the gas spring area) to lubricate the seals properly?
Any advice is appreciated. Thanks.