mogun
New member
- May 5, 2024
- 3
Hi everyone,
Think about a hydraulic system with series of a pump, hose and two valve. pump is working with 3000 psi. First I closed v2 valve and right after that I closed the v1. what happen to pressure of the hydraulic fluid between v1 and v2 valve?
Think about a hydraulic system with series of a pump, hose and two valve. pump is working with 3000 psi. First I closed v2 valve and right after that I closed the v1. what happen to pressure of the hydraulic fluid between v1 and v2 valve?
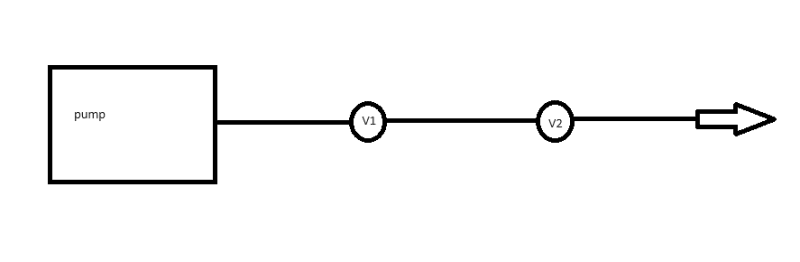