KootK
Structural
- Oct 16, 2001
- 18,563
I have the opportunity to be involved in a substantial amount of guard rail testing on some mid-rise, Canadian, PT buildings. I've not done this before but, as a budding entrepreneur, I don't consider myself to have the luxury of sticking to things that I already know how to do. For what it's worth, I'm in the proposal stage at the moment. I also have a couple of good resources (ASTM E935-13 an CSA A500-16). I've scanned them in search of my answers but I'm afraid that I don't have time this week to do any deep reading. I'd be mighty grateful for any help that anyone can offer with respect to the following questions:
1) When looking at a bunch of guardrails, what percentage needs to be tested in order to establish statistical significance? A500 seems to say "depends on how many" but then seems to imply two or three per installation configuration.
2) Where does one get the equipment for the test and how much does is cost to buy or rent?
3) What's a reasonable time allotment for the execution of a single guard test in the field?
4) Obviously, any other relevant standards or reference material would be appreciated.
In addition to the standards that I mentioned, I've got this which is decent: (Link). I know there's at least on good thread out there with Ron contributing but I'm at a loss to track it down so far.
I like to debate structural engineering theory -- a lot. If I challenge you on something, know that I'm doing so because I respect your opinion enough to either change it or adopt it.
1) When looking at a bunch of guardrails, what percentage needs to be tested in order to establish statistical significance? A500 seems to say "depends on how many" but then seems to imply two or three per installation configuration.
2) Where does one get the equipment for the test and how much does is cost to buy or rent?
3) What's a reasonable time allotment for the execution of a single guard test in the field?
4) Obviously, any other relevant standards or reference material would be appreciated.
In addition to the standards that I mentioned, I've got this which is decent: (Link). I know there's at least on good thread out there with Ron contributing but I'm at a loss to track it down so far.
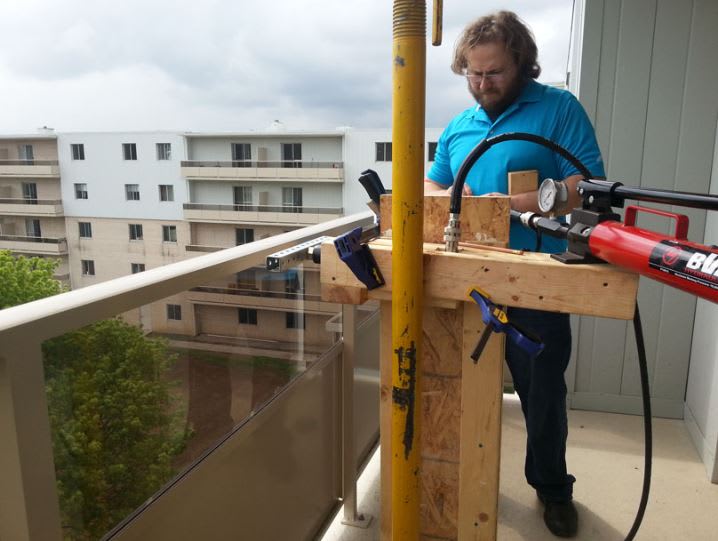
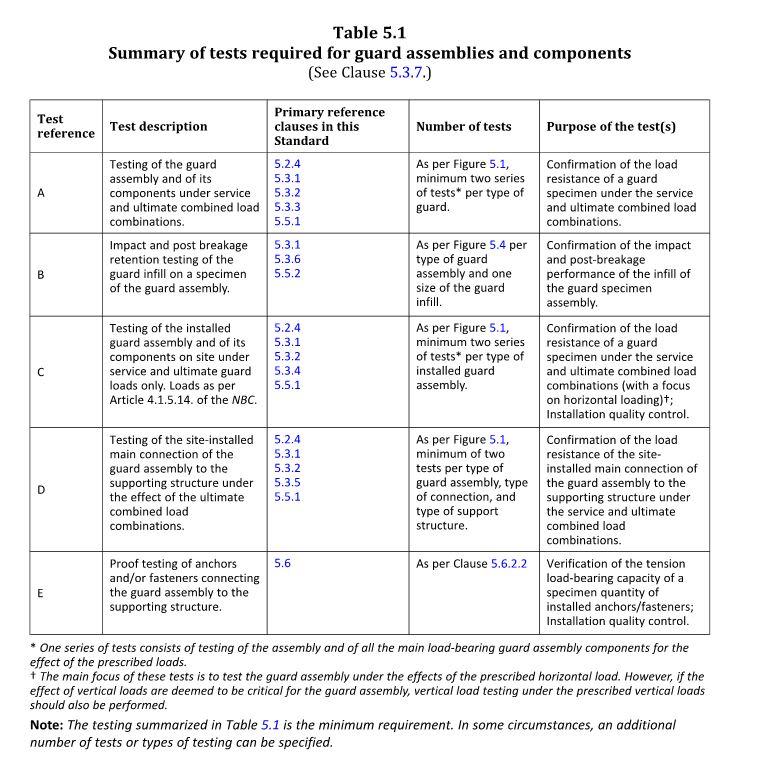
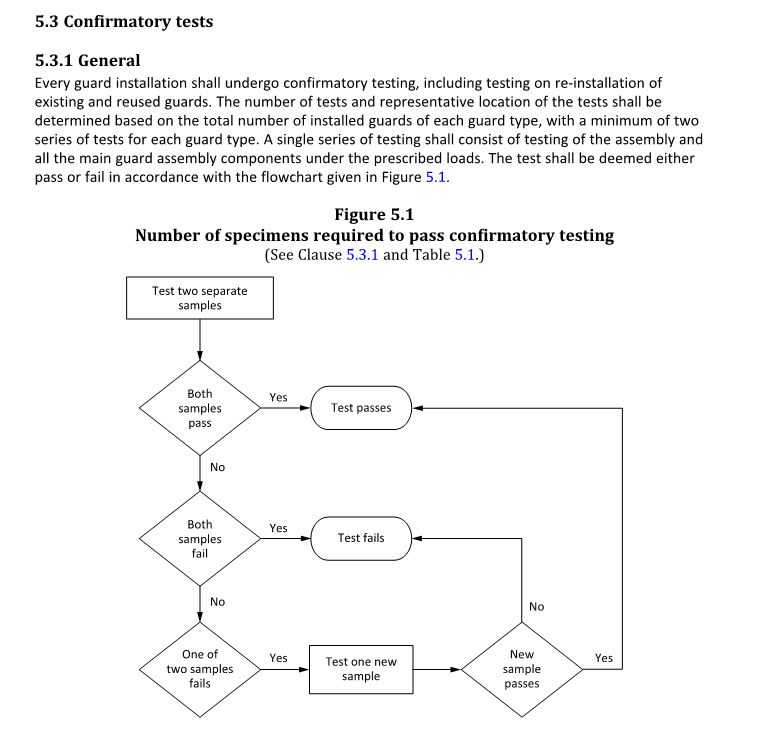
I like to debate structural engineering theory -- a lot. If I challenge you on something, know that I'm doing so because I respect your opinion enough to either change it or adopt it.