PYA92130
Civil/Environmental
- Oct 2, 2023
- 6
I have designed guard rails based on the AWC prestige method. However, City plan checker want me to provide a structural calculations to show it meet 200lb concentrated load. However, when I treat both bolt as point of support, I got some larger load due to moment. I think I must wrong in the beginning. but I can't figure out yet.
Anyone can help me?
Anyone can help me?
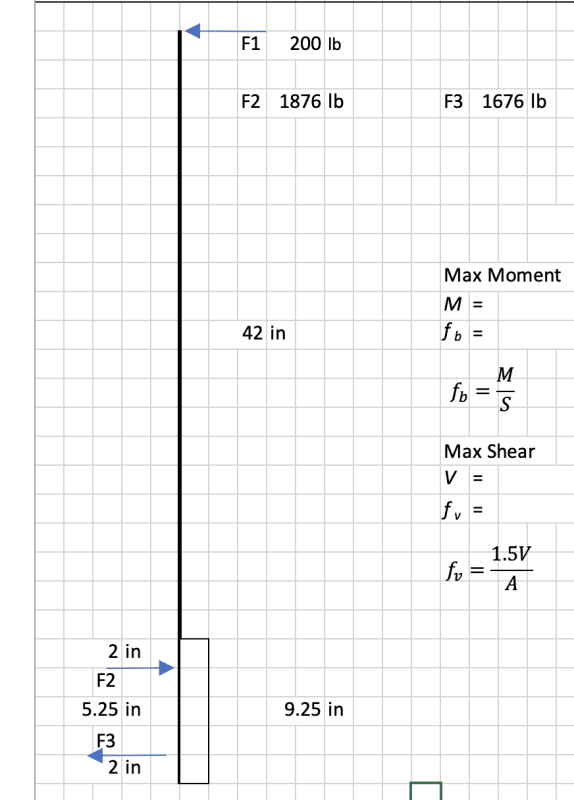
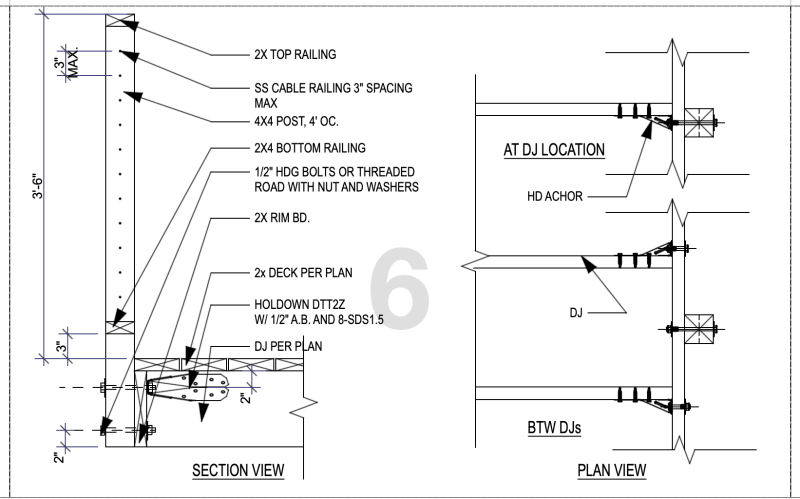