SinStrucEng
Structural
Hi folks. I've got an interesting break in a truss. One of the webs is completely split along its full length. All other truss sections are solid and in good condition. No idea how this would have even happened. Perhaps someone hit the web member during a reno, or sat on it, or something else. No signs of stress in the roof otherwise and it's mint throughout.
How would you personally go about fixing this?
I have ideas but I am concerned about constructibility. In my opinion the whole web member needs to be replaced. I propose cutting it out, carefully, without damaging the nail plates, then inserting a new piece of matching size (2x3) in its stead. Then install plywood/OSB gusset plates at the top and bottom connections over the existing nail plates as surety.
My concern is the contractor:
1) damaging the nail plates and most importantly
2) getting the new member in at full length, particularly without bending removing the existing nail plates.
Maybe cut the nail plate to be able to slot the new piece in and then gusset over it all?
How would you personally go about fixing this?
I have ideas but I am concerned about constructibility. In my opinion the whole web member needs to be replaced. I propose cutting it out, carefully, without damaging the nail plates, then inserting a new piece of matching size (2x3) in its stead. Then install plywood/OSB gusset plates at the top and bottom connections over the existing nail plates as surety.
My concern is the contractor:
1) damaging the nail plates and most importantly
2) getting the new member in at full length, particularly without bending removing the existing nail plates.
Maybe cut the nail plate to be able to slot the new piece in and then gusset over it all?
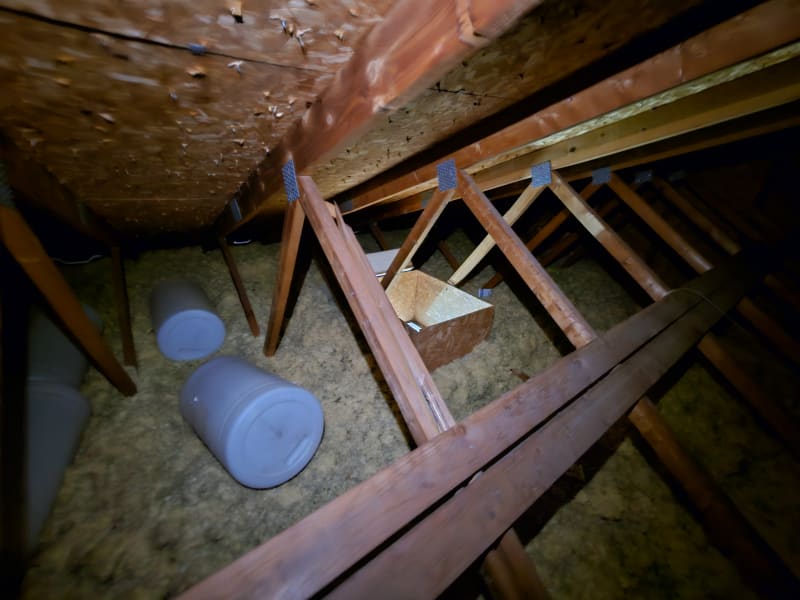
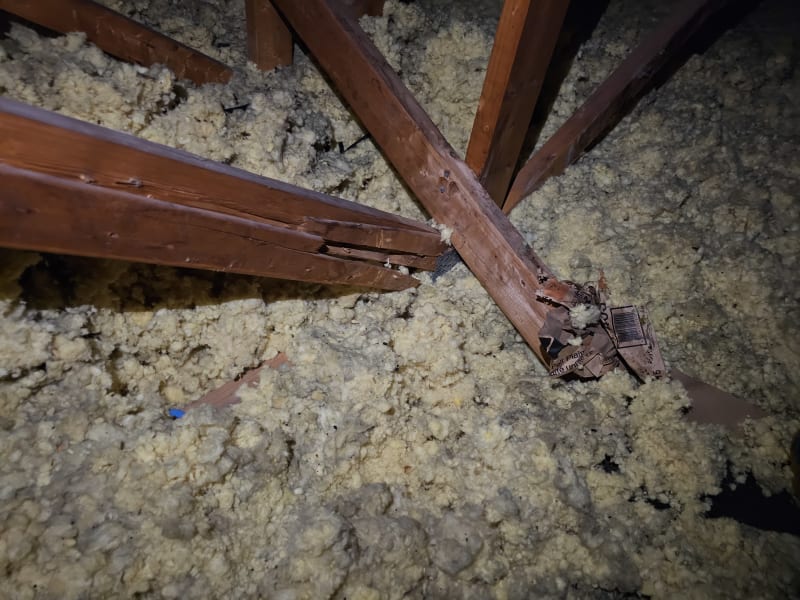
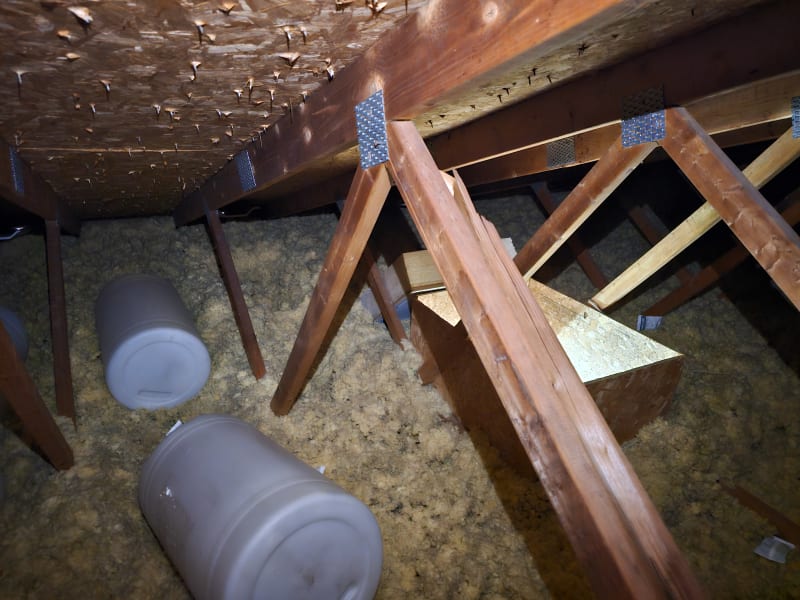
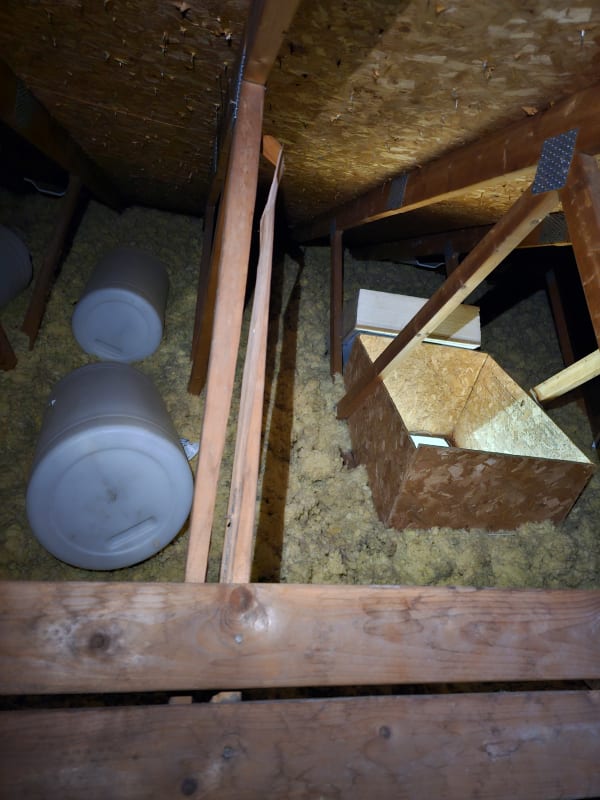