Hi all
For an internal snap ring with two grip holes that we get from a supplier, we need to control three dimensions and it seems hard that all of these parameters come right at the same time. The dimensions interested are: the horizontal inter-axis of the two holes, the vertical inter-axis between the holes and the center of the ring and the Ring diameter. There's also a spring back included.
regarding to the production method of the ring that I don't think that would be more than one method, is there any control method during production to apply to avoid these diameters go into discordance with the required?
For an internal snap ring with two grip holes that we get from a supplier, we need to control three dimensions and it seems hard that all of these parameters come right at the same time. The dimensions interested are: the horizontal inter-axis of the two holes, the vertical inter-axis between the holes and the center of the ring and the Ring diameter. There's also a spring back included.
regarding to the production method of the ring that I don't think that would be more than one method, is there any control method during production to apply to avoid these diameters go into discordance with the required?
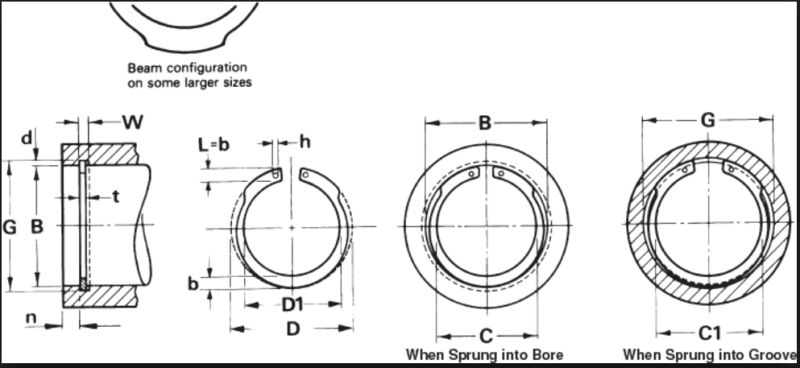