JesseLou
Mechanical
- Aug 15, 2023
- 3
Hey all,
I can't find much information on this at all.... Even in the ASME standard.. Only a couple pages on patterns as datums.
So... I have a irregular pattern that I am picking up the top of to make Datum-D and then I want to make the pattern itself Datum-E so we can check a few holes relative to this pattern...
Question1: If there was not DRF(datum reference frame) origin called out, where would it be for Datum-E, the 7x bolt pattern?
Question2: What would be the best way to locate it?
Could I put it wherever I want and just draw some basic dimensions from the red centerline ( which I manually made)??
I can't find much information on this at all.... Even in the ASME standard.. Only a couple pages on patterns as datums.
So... I have a irregular pattern that I am picking up the top of to make Datum-D and then I want to make the pattern itself Datum-E so we can check a few holes relative to this pattern...
Question1: If there was not DRF(datum reference frame) origin called out, where would it be for Datum-E, the 7x bolt pattern?
Question2: What would be the best way to locate it?
Could I put it wherever I want and just draw some basic dimensions from the red centerline ( which I manually made)??

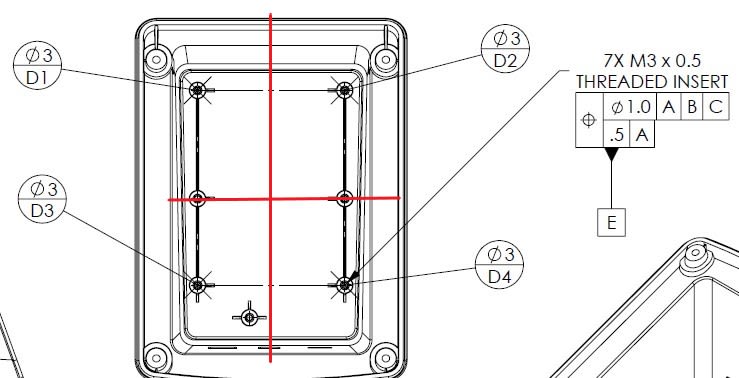