I am looking to jack up a process vessel / tank / silo on load cells. The purpose to move the tanl just a few milimeters to help verify the accuracy of the load cells. I am in the process weighing vessel industry and know nothing about hydraulics.
Whay I hope to do is to have a manual pump connected to a 6 port manifold with one hose connected to the pump, one hose connected to a pressure gage and 4 hoses connected to the jacks at each of the 4 lifting points. Between the jack and the load will be the a load cell that is part of the measurement system electronics.
The process would be to start with a fully loaded tank. Excersise the hand pump until contact is made and registered on the measuruing system electronics. Repeat for all 4 measurement points. Zero the system under test readout, zero the verification electronicc. Increase the hydraulic pressure in small increments and verify that the unit unde test matches the readings of the verification electronics. The test electronics indincation will increase and the system under test will decrease. If not introduce a calibration factor and repeat the test.
My questions are about equipment selection for the hydraulic components. My goal is to have four 20 ton low profile jacks.
This would give me 80 ton lift capability * 0.8 for a safe lift capacity of 64 tons.
1- For a slow manual process like this with a very low duty cycle, (maybe used a few times a year) what is the most important features or specifications are most important when selecting the jacks?
2- How to select the correct hoses / fittings?
3- any general suggestions / precautions.
I see 20 ton jacks for 500 dollars and cheaper ones for 100 dollars on Amazon, what is the difference between these ?
Whay I hope to do is to have a manual pump connected to a 6 port manifold with one hose connected to the pump, one hose connected to a pressure gage and 4 hoses connected to the jacks at each of the 4 lifting points. Between the jack and the load will be the a load cell that is part of the measurement system electronics.
The process would be to start with a fully loaded tank. Excersise the hand pump until contact is made and registered on the measuruing system electronics. Repeat for all 4 measurement points. Zero the system under test readout, zero the verification electronicc. Increase the hydraulic pressure in small increments and verify that the unit unde test matches the readings of the verification electronics. The test electronics indincation will increase and the system under test will decrease. If not introduce a calibration factor and repeat the test.
My questions are about equipment selection for the hydraulic components. My goal is to have four 20 ton low profile jacks.
This would give me 80 ton lift capability * 0.8 for a safe lift capacity of 64 tons.
1- For a slow manual process like this with a very low duty cycle, (maybe used a few times a year) what is the most important features or specifications are most important when selecting the jacks?
2- How to select the correct hoses / fittings?
3- any general suggestions / precautions.
I see 20 ton jacks for 500 dollars and cheaper ones for 100 dollars on Amazon, what is the difference between these ?
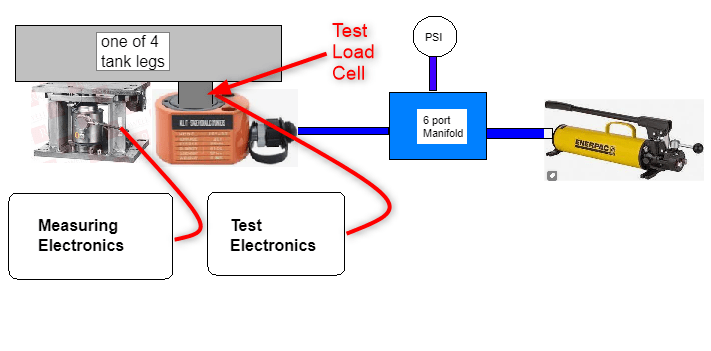