jsu0512
Structural
- Aug 1, 2017
- 32
I'm reviewing the screw that anchor the aluminum jamb of a swing door to the supporting structure and i'd like your opinon on the screw design.
My engineering colleague believes that the screws that anchor the door's jamb to the substrate should be designed for prying-tension load due to the twisting along the jamb created by load eccentricity between the glazing gasket (where the glass bears) and the mullion-to-substrate interface. And that approach would lead to very tight screw spacing...
My view is that the door's jamb wouldn't twist like he believe because door jamb is tied to header / sill frame rotational restraint that jamb can't rotate; the jamb, header and sill frame would work together as one stiff rigid portal frame. With that twisting locked up, the perimeter screws would carry shear load only. I'm attempting to demonstrate this to him by (1) showing that the head/sill to jamb screw connection provide adequate rotational restraint relative to the twisting moment and (2) verifying that the jamb's torsional strength greater than the calculated twisting moment demand.
Does treating the door portal frame as rigid and therefore designing the perimeter screw for shear load alone seems reasonable to you, or should i account for prying tension load as my colleague suggest?
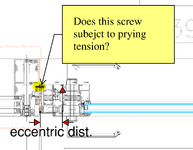
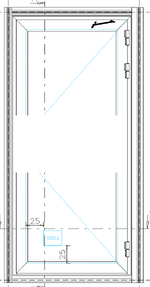
My engineering colleague believes that the screws that anchor the door's jamb to the substrate should be designed for prying-tension load due to the twisting along the jamb created by load eccentricity between the glazing gasket (where the glass bears) and the mullion-to-substrate interface. And that approach would lead to very tight screw spacing...
My view is that the door's jamb wouldn't twist like he believe because door jamb is tied to header / sill frame rotational restraint that jamb can't rotate; the jamb, header and sill frame would work together as one stiff rigid portal frame. With that twisting locked up, the perimeter screws would carry shear load only. I'm attempting to demonstrate this to him by (1) showing that the head/sill to jamb screw connection provide adequate rotational restraint relative to the twisting moment and (2) verifying that the jamb's torsional strength greater than the calculated twisting moment demand.
Does treating the door portal frame as rigid and therefore designing the perimeter screw for shear load alone seems reasonable to you, or should i account for prying tension load as my colleague suggest?
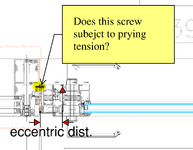
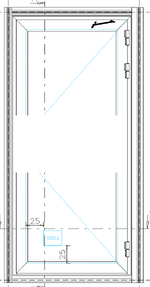