If you have a column with restraints at various levels, how do you prove that restraints are effective?
Mention is made for 2.5% of compression load, but haven't seen an example with variable compression in column with more than one restraint, as per example.
Is there an official accepted method, for determining the restraint force required to pass through each level?
Mention is made for 2.5% of compression load, but haven't seen an example with variable compression in column with more than one restraint, as per example.
Is there an official accepted method, for determining the restraint force required to pass through each level?
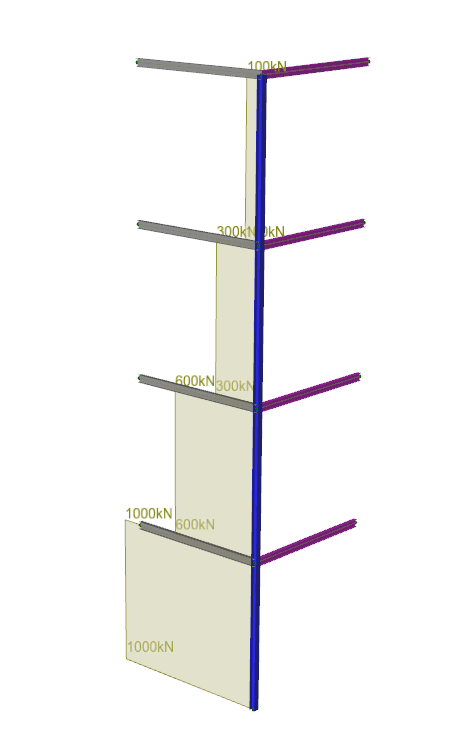