human909
Structural
- Mar 19, 2018
- 2,112
Does anybody have some good references on understanding and dealing with fatigue failure in steel? As I understand it is exacerbated by cyclical stress (obviously) particularly high stress or alternating compression-tension stress.
I ask as I will be looking at this bottom flange & web crack.
I believe it is in an area of hogging moment but likely with enough vibration for it to cycle through compression and tension. It is loaded by heavy vibratory equipment.
I ask as I will be looking at this bottom flange & web crack.
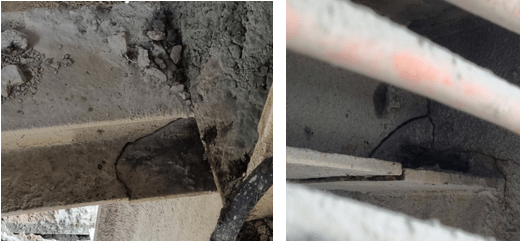
I believe it is in an area of hogging moment but likely with enough vibration for it to cycle through compression and tension. It is loaded by heavy vibratory equipment.