sendithard
Industrial
I'm trying to understand this callout that I think is illegal b/c I always default to physical hard gages.
So this primary datum is the exterior neck diameter of a screw. And the thru hole on the part is the position tolerance callout that uses LMB on datum B.
If you use LMB on an exterior diameter you in essence are saying go grab me the smallest collet that you can at this parts smallest diameter. Therefore, the part could never bounce around inside the collect.
It seems the virtual condition of this diameter datum B is the smallest it could ever be made at, so how can you physically make a gage for this and let the part move around at the same time?
So this primary datum is the exterior neck diameter of a screw. And the thru hole on the part is the position tolerance callout that uses LMB on datum B.
If you use LMB on an exterior diameter you in essence are saying go grab me the smallest collet that you can at this parts smallest diameter. Therefore, the part could never bounce around inside the collect.
It seems the virtual condition of this diameter datum B is the smallest it could ever be made at, so how can you physically make a gage for this and let the part move around at the same time?
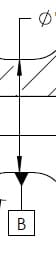
