Hello,
I am investigating the local rotations of rectangular hollow section T-joints under in-plane bending.
I have modelled a chord und a brace which are connected via a tie constraint. The reference point on top is coupled to the top surface of my brace.
Then the RP is loaded with a single moment.
Here you can see my model:
The results look something like that:
My ultimate goal is to get Phi - the local deformation of the joint. I do not want the elastic deformations of the brace Phi_br and the chord Phi_ch.
For now I extract the global rotation - UR1 - of my reference point and substract the values of the elastic rotation of the chord and the brace.
I get those with simple equations (engineering beem teory).
Is there any way to extract just the local joint rotation Phi? If so, could you give me a hint on how to do it.
Thanks!!
I am investigating the local rotations of rectangular hollow section T-joints under in-plane bending.
I have modelled a chord und a brace which are connected via a tie constraint. The reference point on top is coupled to the top surface of my brace.
Then the RP is loaded with a single moment.
Here you can see my model:
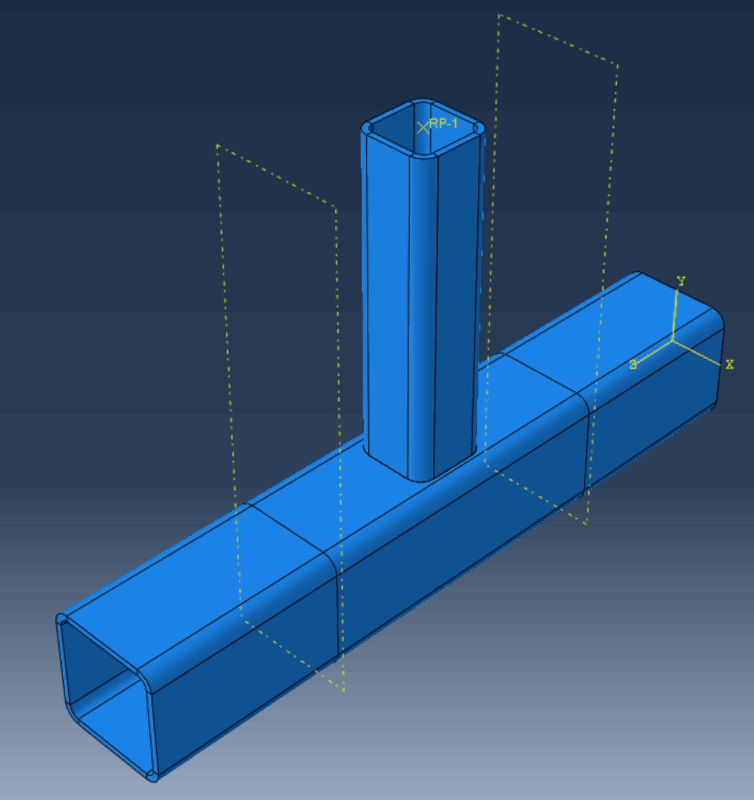
The results look something like that:
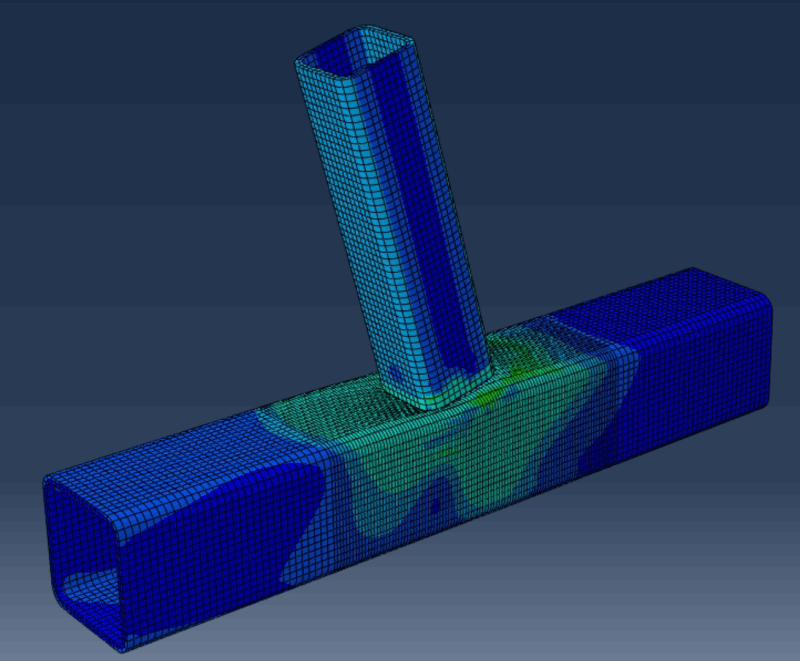
My ultimate goal is to get Phi - the local deformation of the joint. I do not want the elastic deformations of the brace Phi_br and the chord Phi_ch.
For now I extract the global rotation - UR1 - of my reference point and substract the values of the elastic rotation of the chord and the brace.
I get those with simple equations (engineering beem teory).
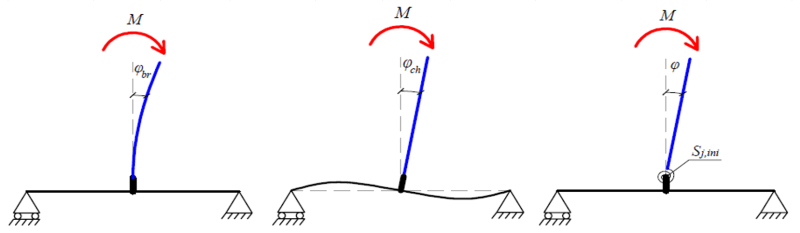
Is there any way to extract just the local joint rotation Phi? If so, could you give me a hint on how to do it.
Thanks!!