Gustavo Silvano
Industrial
- Aug 12, 2016
- 53
Hello there!
I'm an electrical engineer and I just mounted a new machine on my industrie. It's composed of a motor turning a shaft. This turn is made when the operator press a button. But due to the inertia of the shaft, when the motor stop spinning, the shaft make a half of a turn. And this is caused by the fact that the motor does not have a break.
This inertia was not taked into account when I was making the project for this improvement, but I want to fix it without changing the motor. Is there a way to do this? An electrical or mechanical one?
I don't know if it's necessary, but here's the project that was implemented.
Best regards.
Gustavo
I'm an electrical engineer and I just mounted a new machine on my industrie. It's composed of a motor turning a shaft. This turn is made when the operator press a button. But due to the inertia of the shaft, when the motor stop spinning, the shaft make a half of a turn. And this is caused by the fact that the motor does not have a break.
This inertia was not taked into account when I was making the project for this improvement, but I want to fix it without changing the motor. Is there a way to do this? An electrical or mechanical one?
I don't know if it's necessary, but here's the project that was implemented.
Best regards.
Gustavo
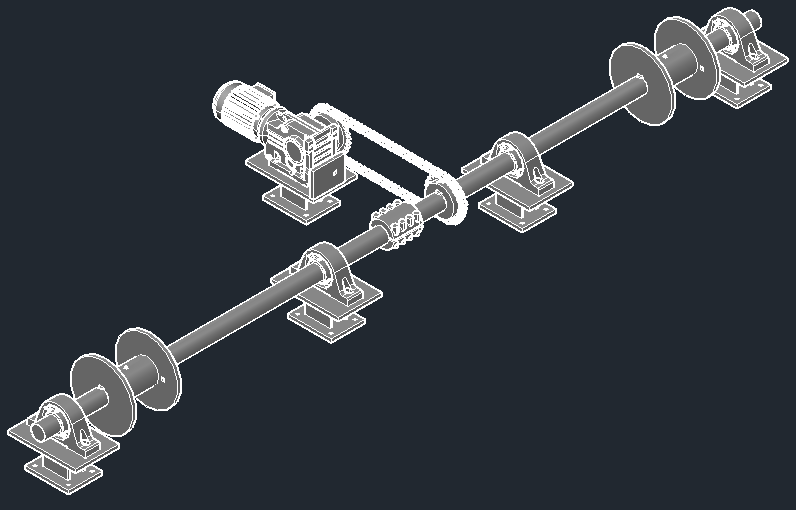