Pavan Kumar
Chemical
- Aug 27, 2019
- 397
Dear All,
I have a process problem that I am trying solve. The Condensate from one side of the plant is sent to Flash Tank, flash steam separated by venting to atmosphere and the LP condensate is pumped to DN 50 (2"NPS) Condensate Header that has Condensate Flash Steam. The question is will the 2" Condensate header be overloaded resulting in high back pressure. This being done per Client's need who has asked as to check the feasibility. The input is provided below.
HP Condensate from Plant = 2534 kg/hr
Pressure upstream of Steam Traps = 10 bar(g)
Flash Tank Operating Pressure = 0 bar(g)
Condensate Header size = DN 50
Condensate Header Pressure = 0 bar(g)
Condensate Load = 254 kg/hr
Pressure upstream of Steam Traps = 12 bar(g)
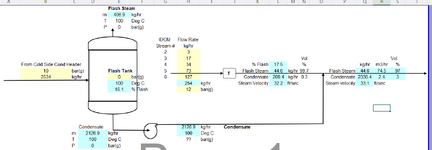
My calculations are shown attached in the spreadsheet. The methodology I used (which I want to cross-check with you) is as follows:
1. Determine the % Flash in the 2" Condensate based on pressure reduction from, 12 bar(g) to 0 bar(g)
2. Estimate the Flash Steam Flow Rate and estimate the Flash Steam Velocity.
3. Estimate the % volume of Flash Steam and Condensate in the 2" pipe using the specific volumes of Flash Steam and Condensate.
4. Add the Condensate from Flash Tank and determine the new volume % of Flash Steam and Condensate.
5. Estimate the increase in the Condensate Liquid level and thereby estimate the reduced cross-sectional flow area for Flash Steam and thus the new Steam Velocity.
6. Check if this new steam velocity is still less than 15-20 m/sec recommended Flash Steam velocity in condensate return lines.
Your comments and resources will be helpful.
Thanks and Regards,
Pavan Kumar
I have a process problem that I am trying solve. The Condensate from one side of the plant is sent to Flash Tank, flash steam separated by venting to atmosphere and the LP condensate is pumped to DN 50 (2"NPS) Condensate Header that has Condensate Flash Steam. The question is will the 2" Condensate header be overloaded resulting in high back pressure. This being done per Client's need who has asked as to check the feasibility. The input is provided below.
HP Condensate from Plant = 2534 kg/hr
Pressure upstream of Steam Traps = 10 bar(g)
Flash Tank Operating Pressure = 0 bar(g)
Condensate Header size = DN 50
Condensate Header Pressure = 0 bar(g)
Condensate Load = 254 kg/hr
Pressure upstream of Steam Traps = 12 bar(g)
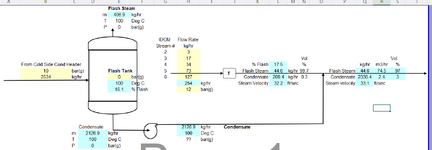
My calculations are shown attached in the spreadsheet. The methodology I used (which I want to cross-check with you) is as follows:
1. Determine the % Flash in the 2" Condensate based on pressure reduction from, 12 bar(g) to 0 bar(g)
2. Estimate the Flash Steam Flow Rate and estimate the Flash Steam Velocity.
3. Estimate the % volume of Flash Steam and Condensate in the 2" pipe using the specific volumes of Flash Steam and Condensate.
4. Add the Condensate from Flash Tank and determine the new volume % of Flash Steam and Condensate.
5. Estimate the increase in the Condensate Liquid level and thereby estimate the reduced cross-sectional flow area for Flash Steam and thus the new Steam Velocity.
6. Check if this new steam velocity is still less than 15-20 m/sec recommended Flash Steam velocity in condensate return lines.
Your comments and resources will be helpful.
Thanks and Regards,
Pavan Kumar