drodrig
Mechanical
- Mar 28, 2013
- 262
Hi there,
We have to cool down some system at -30C/-22F. We are using ethanol.
In order to distribute the coolant in the different sections we want to build a manifold using Swagelok connectors.
First I thought about taking an stainless steel pipe, cut it and weld some caps with threaded holes for the connectors. Such:
But it would have 275mm/11inches in diameter. Too big and to big mixing volume.
The second idea is taking a square block, drill a big hole almost through (inlet) and then perpendicular holes for the outlets. Such:
What do you think? How is the most convenient way to build a manifold/distributor?
thanks
regards,
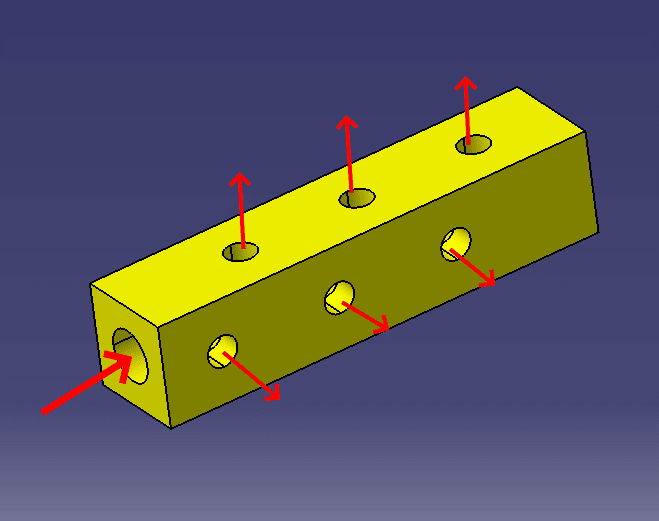
We have to cool down some system at -30C/-22F. We are using ethanol.
In order to distribute the coolant in the different sections we want to build a manifold using Swagelok connectors.
First I thought about taking an stainless steel pipe, cut it and weld some caps with threaded holes for the connectors. Such:
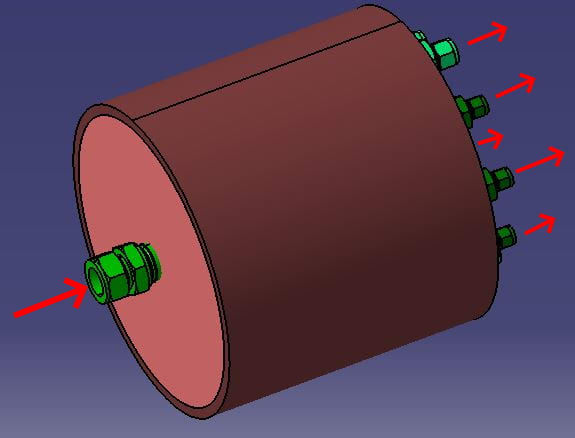
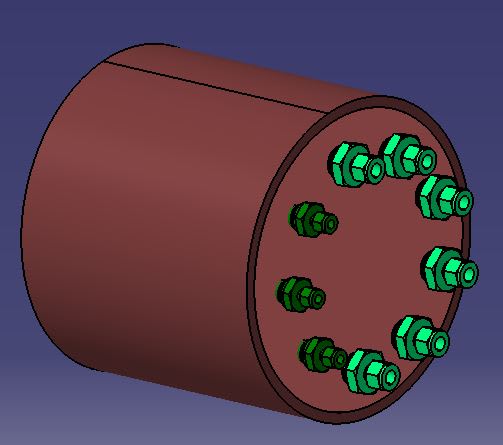
But it would have 275mm/11inches in diameter. Too big and to big mixing volume.
The second idea is taking a square block, drill a big hole almost through (inlet) and then perpendicular holes for the outlets. Such:
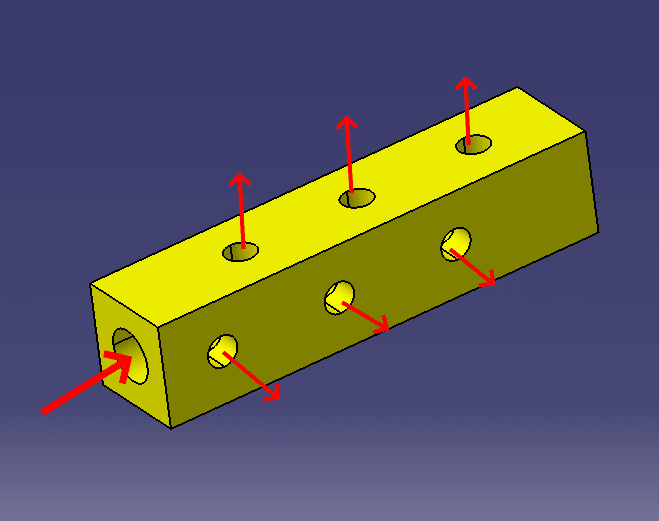
What do you think? How is the most convenient way to build a manifold/distributor?
thanks
regards,