onlym112
Structural
- Sep 9, 2019
- 45
Hello,
I am currently designing a connection where I have an HSS356x254x13 long side vertical into a W310x45 beam which bear on top of a W200x36 Column. This connection is a moment and torsion connection where the torsion is 50 kNm and moment is 60 kNm. I am having a hard time picturing how I will connect this and was wondering if anyone could give me their insight. I have sketched two possibilities however one of them will not work due to a lack of weld access. Please see the pictures of the model and my sketch below.
I also considered an endplate option but I am not allowed to portrude my endplate proud at the top to fit my 1" tension bolts. Also there isn't much guidance on a endplate HSS moment connection and based on the HSS size, things can get real ugly and I am not too sure how to handle it. Can anyone give me some feedback? Thank you very much
I am currently designing a connection where I have an HSS356x254x13 long side vertical into a W310x45 beam which bear on top of a W200x36 Column. This connection is a moment and torsion connection where the torsion is 50 kNm and moment is 60 kNm. I am having a hard time picturing how I will connect this and was wondering if anyone could give me their insight. I have sketched two possibilities however one of them will not work due to a lack of weld access. Please see the pictures of the model and my sketch below.
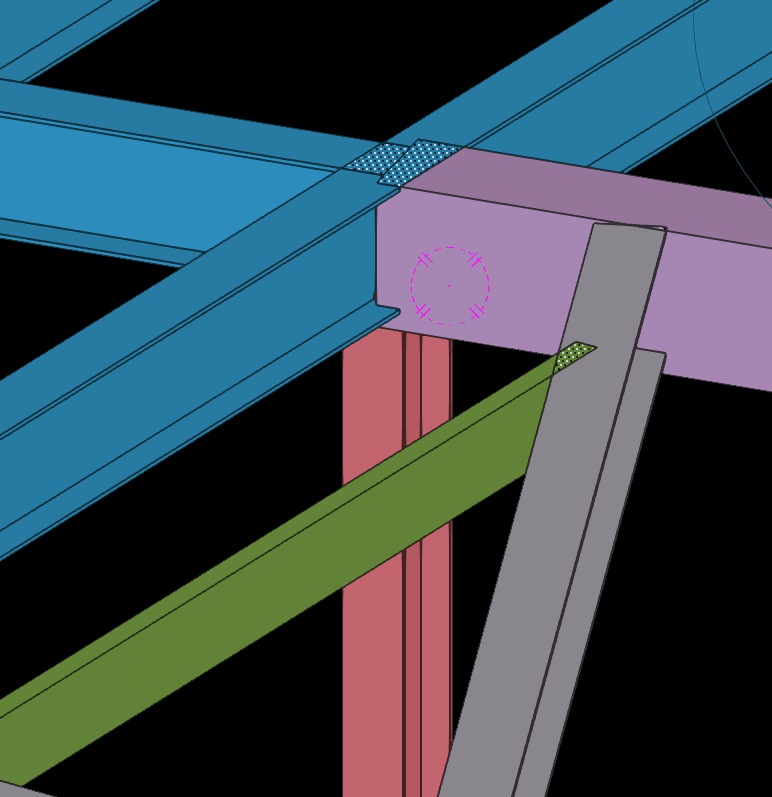
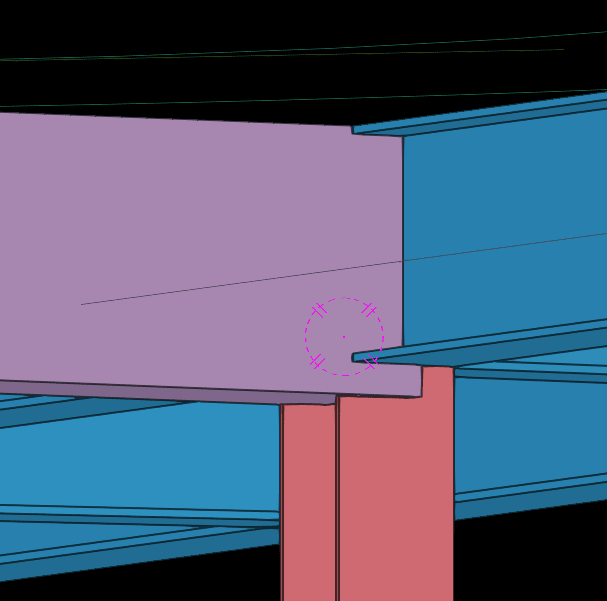
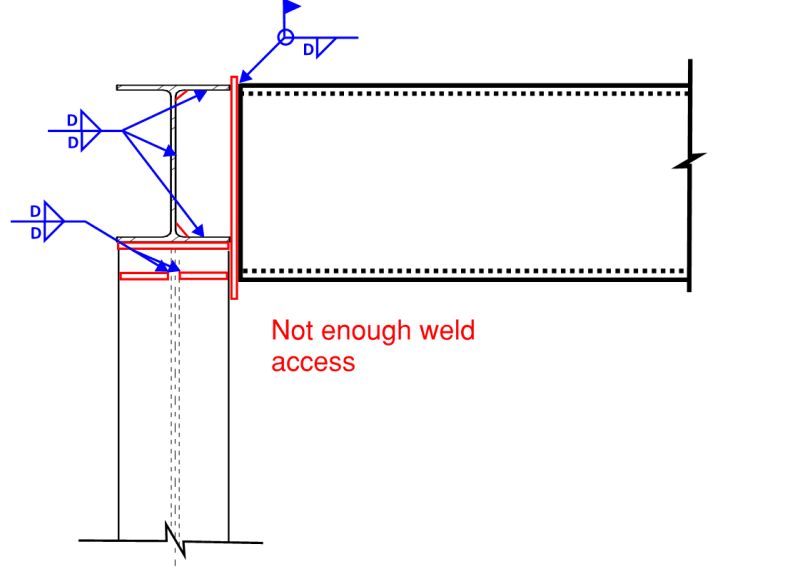
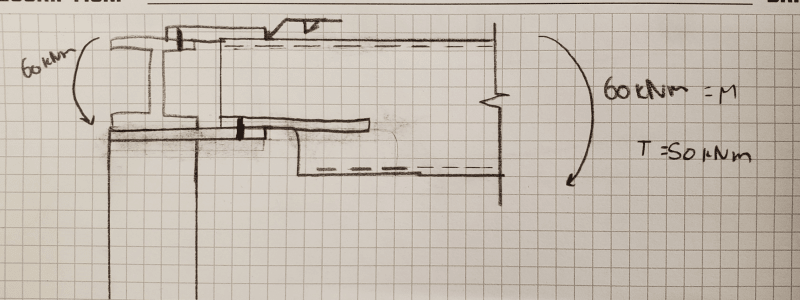
I also considered an endplate option but I am not allowed to portrude my endplate proud at the top to fit my 1" tension bolts. Also there isn't much guidance on a endplate HSS moment connection and based on the HSS size, things can get real ugly and I am not too sure how to handle it. Can anyone give me some feedback? Thank you very much