ALK2415
Structural
- Sep 15, 2014
- 289
Dear Colleagues
What is the practical depth/Span ratio for a Cantilever beam ?
thinking of overhang Plate girders set that cover 60' long [18.3 meters] and 20' wide [6 meters]
thinking of 1/10 ?
this is kind bizarre, but it a monument kind structure, made for main terminal express welcomed sign
similar to this picture [but unbalanced type]
What is the practical depth/Span ratio for a Cantilever beam ?
thinking of overhang Plate girders set that cover 60' long [18.3 meters] and 20' wide [6 meters]
thinking of 1/10 ?
this is kind bizarre, but it a monument kind structure, made for main terminal express welcomed sign
similar to this picture [but unbalanced type]
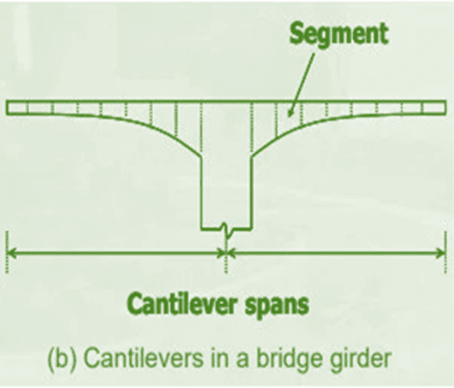