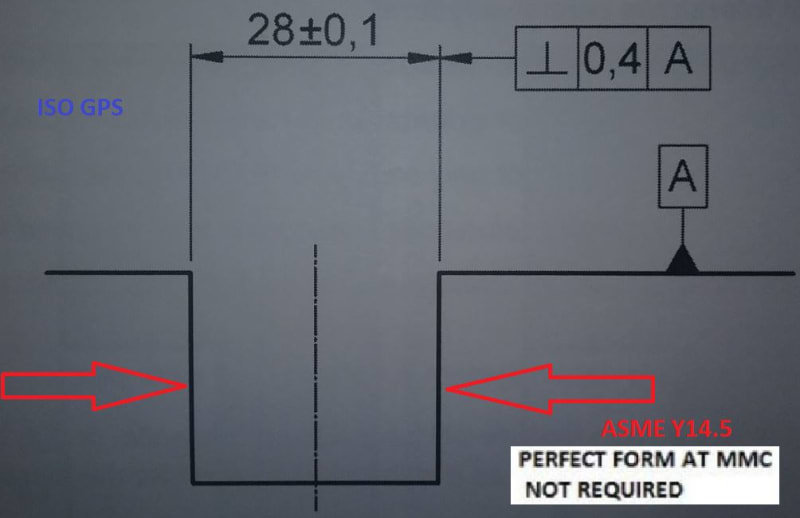
Flatness of the sides shown with red arrows: the combined effect of the two requirements shown (size 28±0.1 and perpendicularity 0.4|A|)
What is the maximum possible flatness error in those 2 cases:
1.) ISO GPS
2.) ASME Y14.5 (with no rule#1 in place)
Is it different or it's the same in both cases and what is the correct value?
I understood that the additional form tolerances can be applied to the shown surfaces (red arrows surfaces) if necessary, but what would be the maximum "as shown" flatness error?