met33
Materials
- Apr 9, 2024
- 29
Can a suspended structural concrete slab be too thick?
I am doing a preliminary "design" of structural cast-in-place concrete porch slabs on my new home, before I find a local structural engineer to do the real design.
The two-way slabs might be 12" thick, and the one-way slabs might be 8" to 12" thick. However, the total spans are relatively short, on the order of 8 feet to 12 feet.
Besides the expense, are there any structural reasons to limit the thickness of structural slabs relative to their span? I'm asking because it seems like the rebar might not be able to do its job if the concrete slab can't deflect enough to engage it. Is that a concern, and could it lead to brittle behavior?
See diagrams below for dimensions.
I am doing a preliminary "design" of structural cast-in-place concrete porch slabs on my new home, before I find a local structural engineer to do the real design.
The two-way slabs might be 12" thick, and the one-way slabs might be 8" to 12" thick. However, the total spans are relatively short, on the order of 8 feet to 12 feet.
Besides the expense, are there any structural reasons to limit the thickness of structural slabs relative to their span? I'm asking because it seems like the rebar might not be able to do its job if the concrete slab can't deflect enough to engage it. Is that a concern, and could it lead to brittle behavior?
See diagrams below for dimensions.
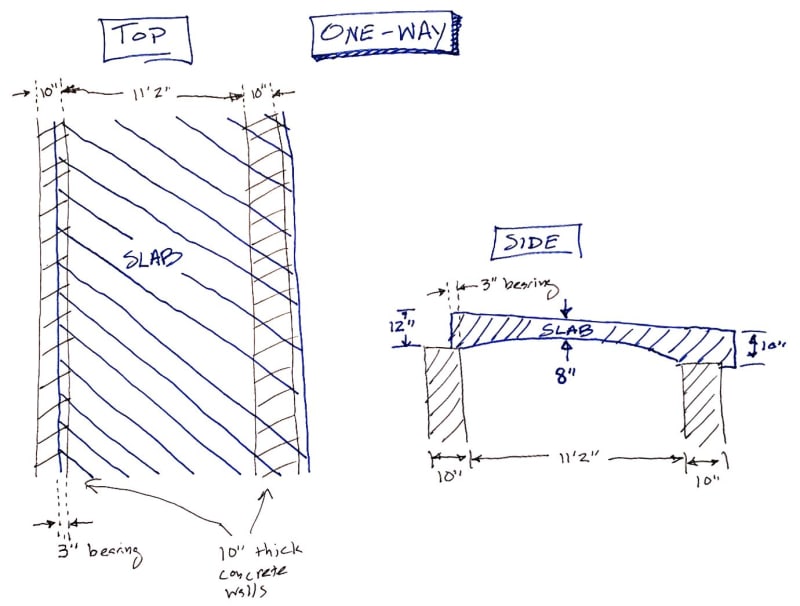
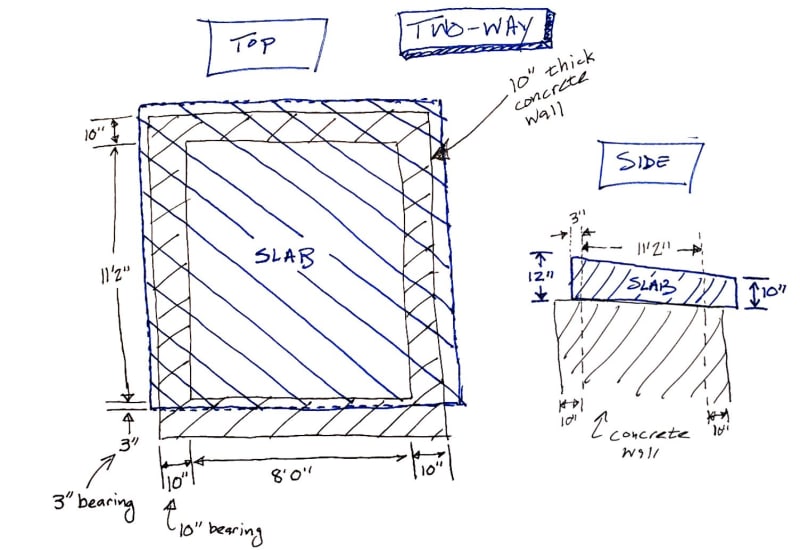