Dear All,
I would like to measure bending moment on tube without measuring all other forces and moments. I am planning to use four strain gauges to measure the bending using full bridges. I am little confused between using tee rosette strain gauges similar to this one and stick it on 45 degree or just use normal strain gauges.
There are forces and moments affects on the tube in all directions, but I want to measure only moment produced from one forces only as shown in the figure. I am not sure which approach is correct to measure the bending and neglect all other forces and moments. See the attached drawing.
I would like to measure bending moment on tube without measuring all other forces and moments. I am planning to use four strain gauges to measure the bending using full bridges. I am little confused between using tee rosette strain gauges similar to this one and stick it on 45 degree or just use normal strain gauges.
There are forces and moments affects on the tube in all directions, but I want to measure only moment produced from one forces only as shown in the figure. I am not sure which approach is correct to measure the bending and neglect all other forces and moments. See the attached drawing.
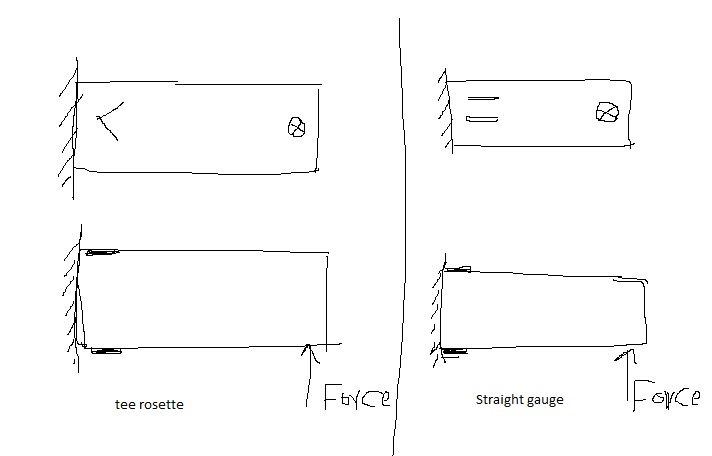