Sicilian Engineer
Mechanical
- Oct 20, 2024
- 9
Hi Engineers,
I am a recent-ish graduate working in a super varied role doing product design. A lot of these products require injection moulded enclosures I have read the bayer guide for df injection moulding but am looking for other tips and general good practice to consider In my work going forward. Generally these cases often need to be water proof, have tons of features, and be impossibly small. I'm going okay with gasket design but often struggle with selecting electrical connectors and other peripherals, as well as good cable routing design.
If anyone has experience in the above area any insights or general tips would be super helpful.
Below I have some more specific problems I was wondering if someone understood best practice for.
In my attached IMG green shows the planned route for a roughly known quantity of ribbon and other cables. I want to put heat-serts in the red and screw in cable clips (already have a bunch from something else). The blue circled 'scallops' I took out of the ribs to allow the cables to pass through as well as guide them somewhat. Essentially I'd like to know if what I am doing is sensible here or if I need to really rethink how and why I'm doing these things.
Anyway thanks anyone for your response or for even reading this mess, any help is appreciated. If anyone is interested in some quid pro quo I am most useful in the world of FFF and SLA printing alongside decent knowledge of machining processes.
Kind Regards,
Chris
I am a recent-ish graduate working in a super varied role doing product design. A lot of these products require injection moulded enclosures I have read the bayer guide for df injection moulding but am looking for other tips and general good practice to consider In my work going forward. Generally these cases often need to be water proof, have tons of features, and be impossibly small. I'm going okay with gasket design but often struggle with selecting electrical connectors and other peripherals, as well as good cable routing design.
If anyone has experience in the above area any insights or general tips would be super helpful.
Below I have some more specific problems I was wondering if someone understood best practice for.
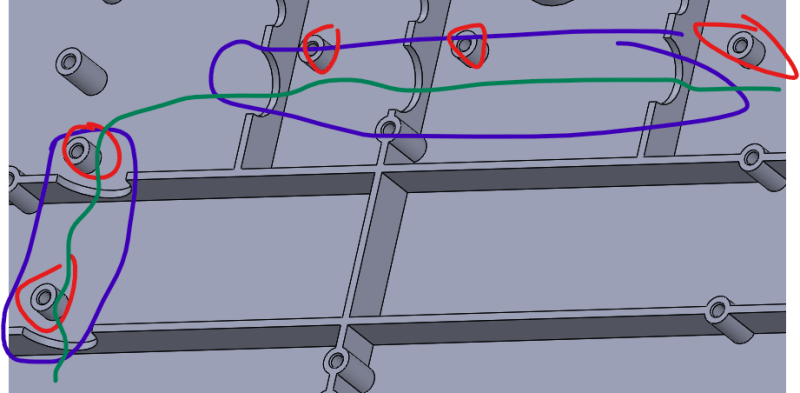
In my attached IMG green shows the planned route for a roughly known quantity of ribbon and other cables. I want to put heat-serts in the red and screw in cable clips (already have a bunch from something else). The blue circled 'scallops' I took out of the ribs to allow the cables to pass through as well as guide them somewhat. Essentially I'd like to know if what I am doing is sensible here or if I need to really rethink how and why I'm doing these things.
Anyway thanks anyone for your response or for even reading this mess, any help is appreciated. If anyone is interested in some quid pro quo I am most useful in the world of FFF and SLA printing alongside decent knowledge of machining processes.
Kind Regards,
Chris