Papabyrd
Mechanical
- Oct 26, 2011
- 18
Hello,
Very stuck with this issue and curious what to do. It has to be something simple.
I've used these pumps (Ingersoll Rand Flowserve SMP-1000 centrifugal) before, 4 times, in a similar application with great success. Now I've installed 5 units where the seal begins to leak within 5 days of operation.
It's pumping Mobile DTE-25 oil. Around 5 gpm. The tank above the pump is ~10 feet and pumping back to it. The last unit we purged all air from the casing from the bleed port, let it sit over the weekend and rebled before operating. When pump/seal was disassembled the components were debris free other than the chewed up rubber.
Seals are viton on the last unit that failed.
The impellers are trimmed down from 4" to 3" at the local distributor shop.
The only other items that come to mind,
a max NPSH, where the above tank pressure overwhelms the mechanical face seal.
The construction of the pump, its also hard to check runnout behind the impellar once installed.
The pump capacity is 30 GPM, running below 5 gpm perhaps doesn't push enough fluid by the seal to cool it.
The hydraulic suction hose is somehow collapsing inside and reducing NPSH.
Seals are confirmed to be installed dry and the oil wicks/capillary into the seal face upon startup. Have not considered prelubing as thast not what is supposed to be done.
Good impeller balancing to be confirmed.
Trying to work with the distributor and manufacturer for support now. It's been going on for 14 months. Frustrated.... Thanks for any thoughts on this.
Very stuck with this issue and curious what to do. It has to be something simple.
I've used these pumps (Ingersoll Rand Flowserve SMP-1000 centrifugal) before, 4 times, in a similar application with great success. Now I've installed 5 units where the seal begins to leak within 5 days of operation.
It's pumping Mobile DTE-25 oil. Around 5 gpm. The tank above the pump is ~10 feet and pumping back to it. The last unit we purged all air from the casing from the bleed port, let it sit over the weekend and rebled before operating. When pump/seal was disassembled the components were debris free other than the chewed up rubber.
Seals are viton on the last unit that failed.
The impellers are trimmed down from 4" to 3" at the local distributor shop.
The only other items that come to mind,
a max NPSH, where the above tank pressure overwhelms the mechanical face seal.
The construction of the pump, its also hard to check runnout behind the impellar once installed.
The pump capacity is 30 GPM, running below 5 gpm perhaps doesn't push enough fluid by the seal to cool it.
The hydraulic suction hose is somehow collapsing inside and reducing NPSH.
Seals are confirmed to be installed dry and the oil wicks/capillary into the seal face upon startup. Have not considered prelubing as thast not what is supposed to be done.
Good impeller balancing to be confirmed.
Trying to work with the distributor and manufacturer for support now. It's been going on for 14 months. Frustrated.... Thanks for any thoughts on this.
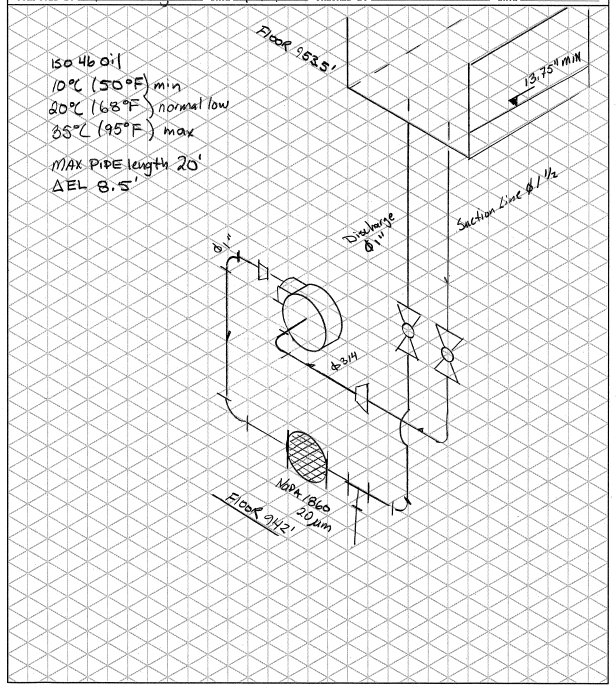
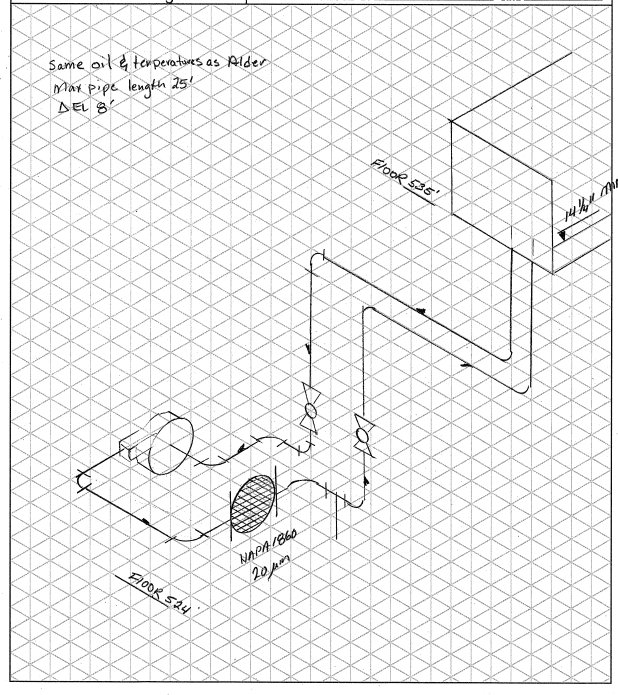
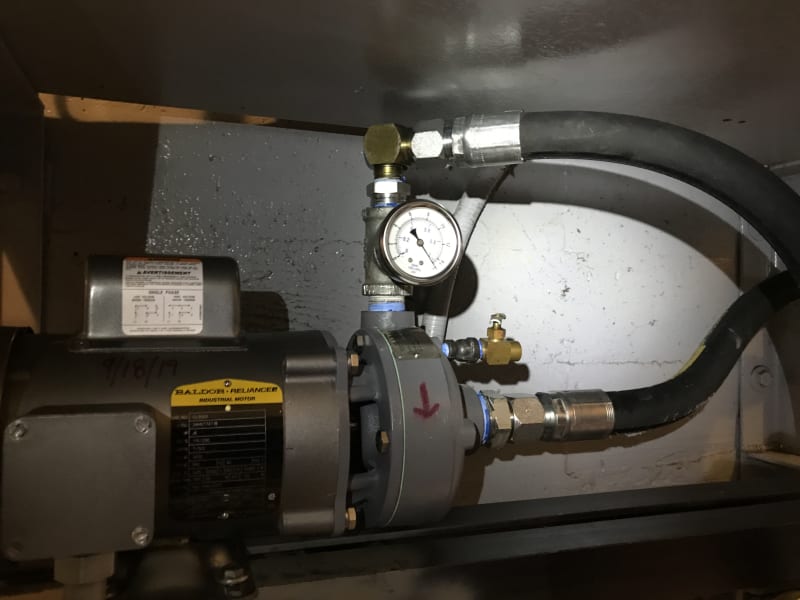
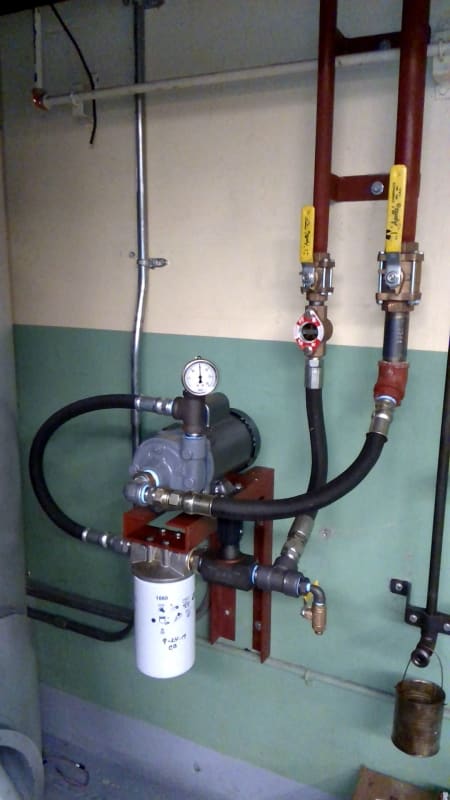
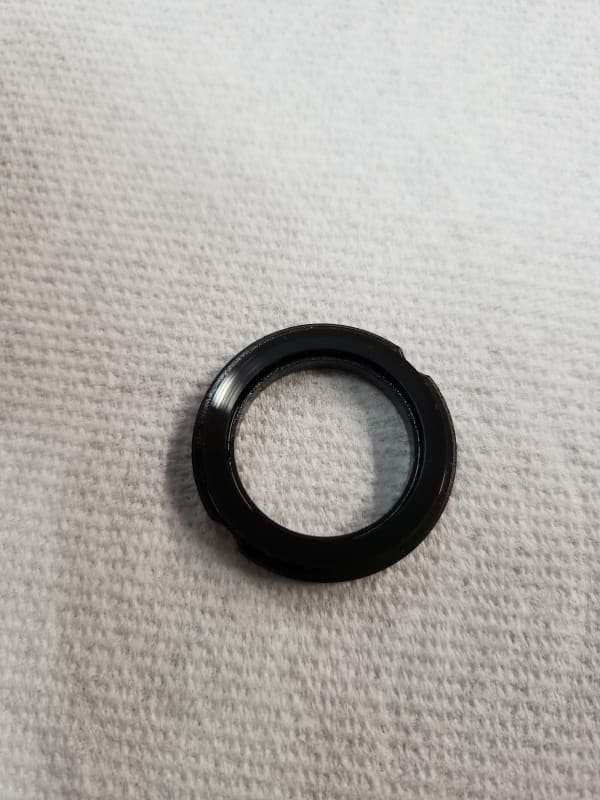
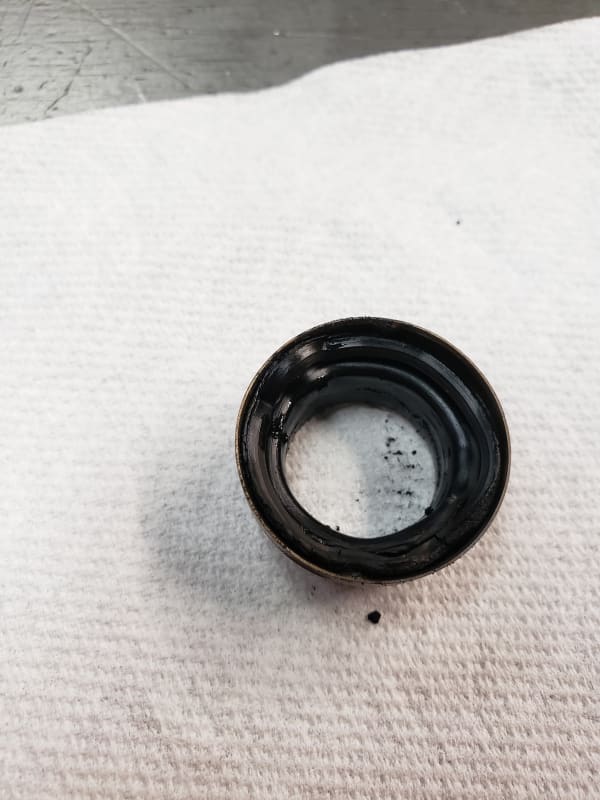
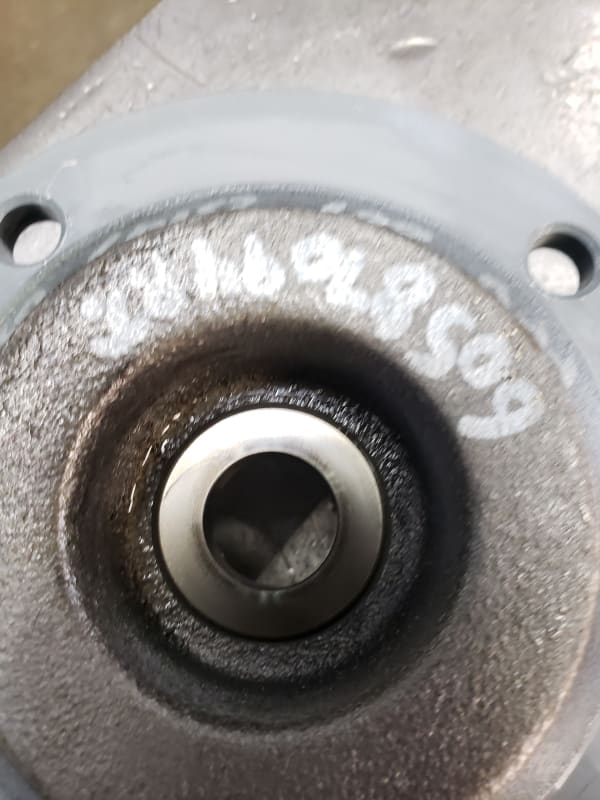
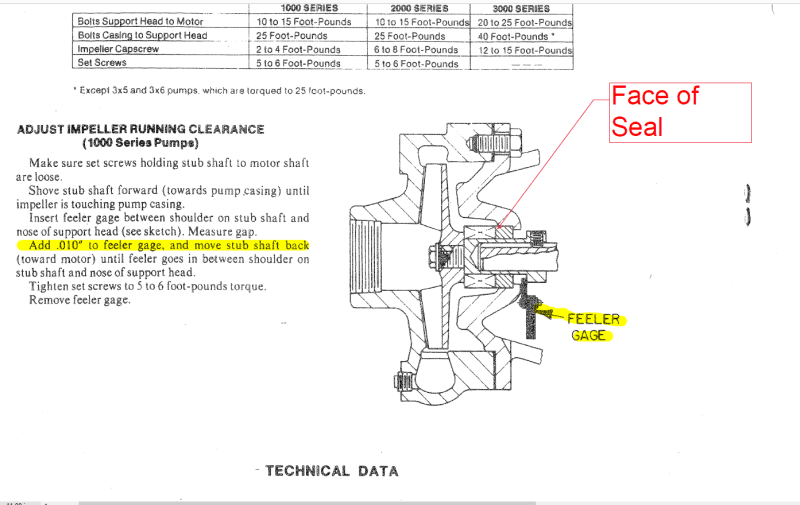
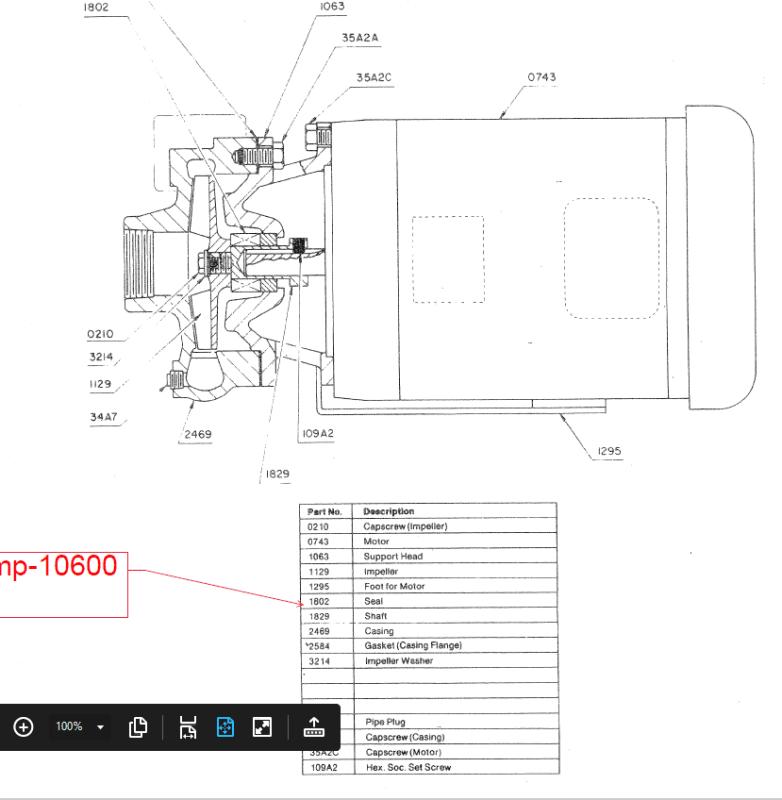