Shahyan
Mechanical
- Jan 28, 2020
- 4
This shell made by metal spinning keeps deforming and I do not know why. There is no problem in the tooling. It is an issue with the material. I do not which mechanical property is the root cause. % elongation 38.4%, maximum tensile strength 426 MPa and yield strength 266.9 MPa. All three properties concur with the standard values. Any help in this matter will be highly appreciated.
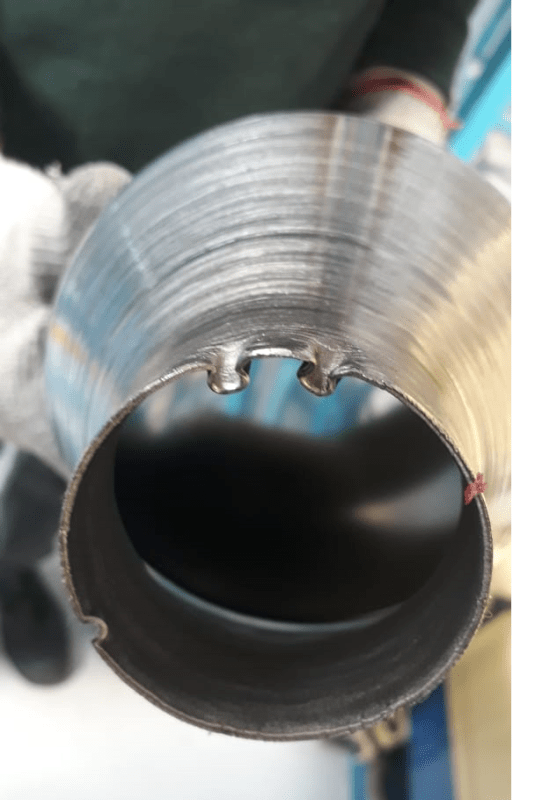