As suggested by the title, I am attempting to model a balloon expansion inside a coronary artery. The balloon is a uniform cylinder, whereas the artery is a non-uniform cylinder (See attached picture). I want to apply a given pressure inside of the balloon, causing it to expand until it touches the vessel. Then, through contact, it should cause the vessel itself to expand with it.
I have specified a contact interaction between the outer surface of the balloon and the inner surface of the vessel. However, when I apply a Pressure Load on the inner surface of the balloon, it ends up ignoring any contact with the vessel and simply expanding as if it were alone.
When I try to apply a Body Force Load instead of Pressure Load, the balloon moves in the specified direction and interacts with the vessel as it should, causing the vessel to also move in the same direction through contact. However, this is not ideal since I cannot make a Body Force act in all directions (as the Pressure Load does).
Does anybody have any tips? Either in how to make the pressure load work or how to apply another type of force that would act in all directions?
I would be happy to provide more details if needed. Thanks!
I have specified a contact interaction between the outer surface of the balloon and the inner surface of the vessel. However, when I apply a Pressure Load on the inner surface of the balloon, it ends up ignoring any contact with the vessel and simply expanding as if it were alone.
When I try to apply a Body Force Load instead of Pressure Load, the balloon moves in the specified direction and interacts with the vessel as it should, causing the vessel to also move in the same direction through contact. However, this is not ideal since I cannot make a Body Force act in all directions (as the Pressure Load does).
Does anybody have any tips? Either in how to make the pressure load work or how to apply another type of force that would act in all directions?
I would be happy to provide more details if needed. Thanks!
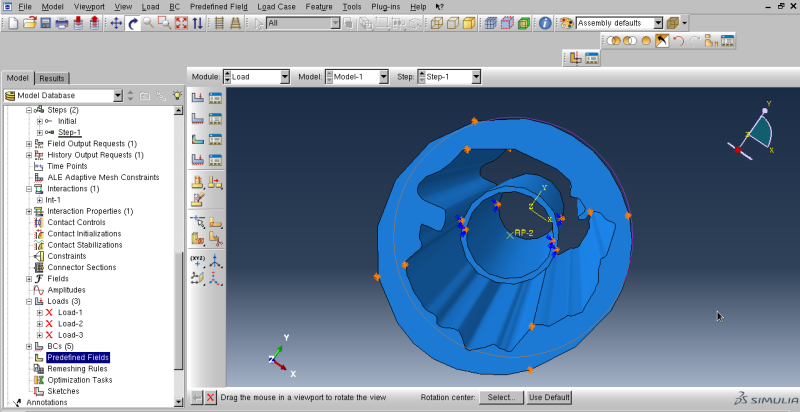