I've got a design that is currently Mold locked. It consists of two mating parts. The issue is with the Female part. I know by opening the bottom, it can be made and by eliminating that undercut.
I'm looking for some suggestions on how to make this design work. The design can change, but the intent is a "twist-fit" connection that must be removable, multiple times. Must be a Robust connection.
Thanks in advance.
Chad
I'm looking for some suggestions on how to make this design work. The design can change, but the intent is a "twist-fit" connection that must be removable, multiple times. Must be a Robust connection.
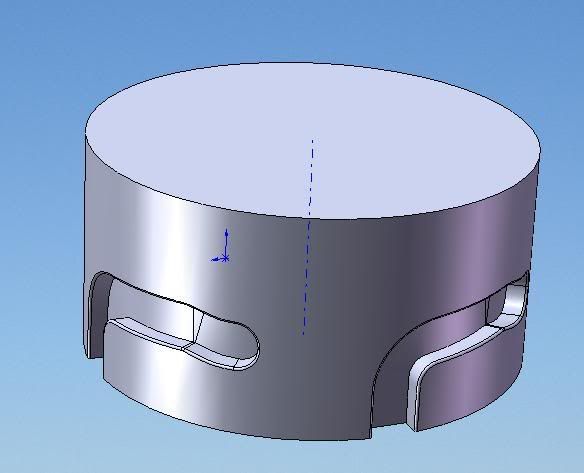
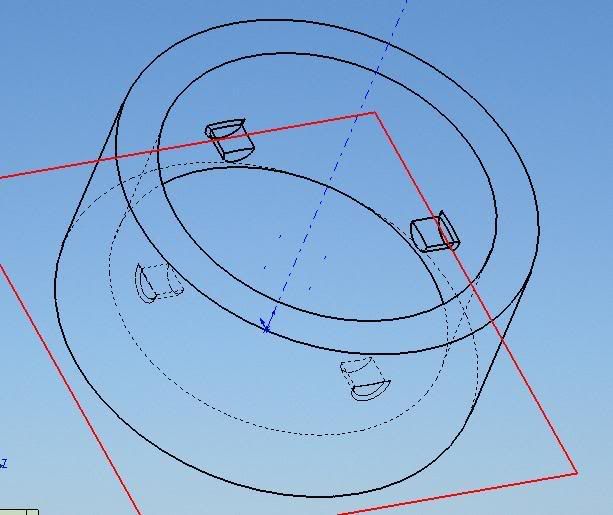
Thanks in advance.
Chad