struct_eeyore
Structural
- Feb 21, 2017
- 264
Hi all,
Need a sanity check. I'm generally against moment connections in wood, but here I have to evaluate someone else's work, so obviously don't want to make too much of a fool out of myself. Please see the attached image below (or wherever it ends up). We've got an open building; the trusses rest on 2x beams which are then secured to columns with 2 thru bolts. The trusses themselves are secured to the 2x beams with 2 USP clips. Now, I can get the portals to work if I resolve the moment across all the straps, of all the trusses. The question is, will that happen in reality, or will the moment likely to want to distribute itself thru the closest straps to the posts? Also, despite the fact that the clips can carry the couple moment, do you think they are rigid enough
Need a sanity check. I'm generally against moment connections in wood, but here I have to evaluate someone else's work, so obviously don't want to make too much of a fool out of myself. Please see the attached image below (or wherever it ends up). We've got an open building; the trusses rest on 2x beams which are then secured to columns with 2 thru bolts. The trusses themselves are secured to the 2x beams with 2 USP clips. Now, I can get the portals to work if I resolve the moment across all the straps, of all the trusses. The question is, will that happen in reality, or will the moment likely to want to distribute itself thru the closest straps to the posts? Also, despite the fact that the clips can carry the couple moment, do you think they are rigid enough
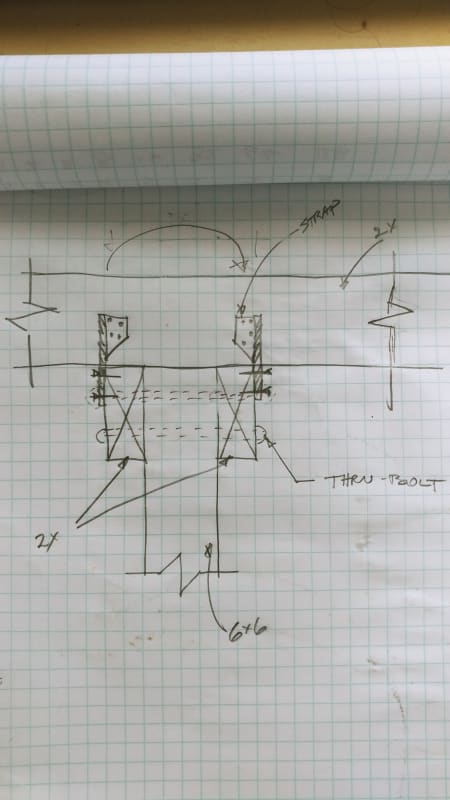