Thunwa
Civil/Environmental
- Jan 29, 2020
- 1
In 2-D, we can distribute moment at any joint by using EI/L of each connected member. So, I tried to distribute moment in 3-D based on 2-D theory but my result did not match the result from RISA-3D. Could you please provided me how to distribute moment in 3 dimensional?
Example for 2-D structure
Example for 3-D structure
Thank you all a lot for your help.![[bigsmile] [bigsmile] [bigsmile]](/data/assets/smilies/bigsmile.gif)
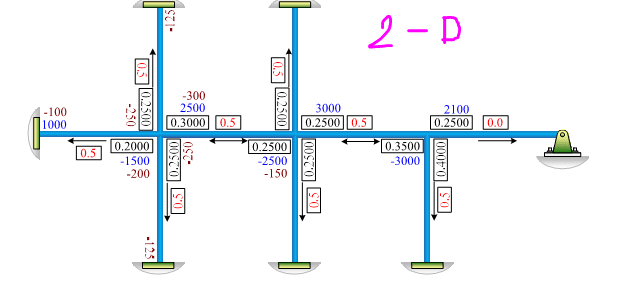
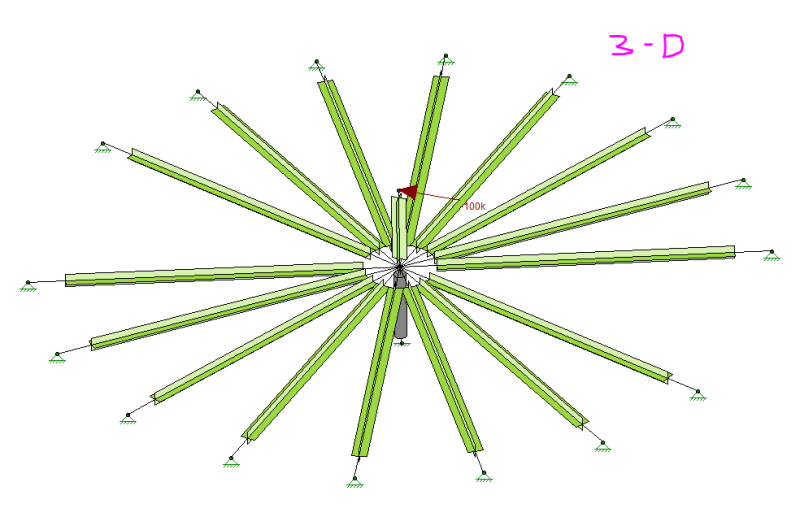
Thank you all a lot for your help.
![[bigsmile] [bigsmile] [bigsmile]](/data/assets/smilies/bigsmile.gif)