T_Bat
Structural
- Jan 9, 2017
- 213
Hey everyone,
I'm looking at a monumental stair design. The stair spans about 33' measured on the flat and has a rise of 18' total. It's one span with no opportunity for posts and is about 7' wide. I've got some relatively large HSS stringers on each end (HSS16x4). The pans will be at least 3/16" thick and will have closed risers. Strength and deflection aren't really an issue - but I'm concerned about vibrations. I used the simplified models from the new AISC DG11 for stairs but they are requiring some very large stringers.
I'm trying to capture the actual (or reasonably close) frequencies for this in RISA. Short of modelling every pan, I've done the following:
1. I've modeled flat plates between the stringers to capture the deep beam action for horizontal sway.
2. I've modeled small L3x3 angles between the stringers at intermittent locations matching the plate nodes. I can run the model without these but I get a lot of local mode shapes for the plates themselves. I consider these extraneous to what I'm doing. The angles modeled basically eliminate these modes and I feel this is reasonably accurate because I'll have a closed riser and pan assembly that creates an angle anyways. Although my modeled angles aren't as often as I'd have risers.
3. As a design note, there are HSS tubes hanging from the stringers to carry a wall. I've modeled these because I feel, if detailed properly, these will help stiffen the stringer for vertical movement - think some vierendeel truss action.
The first mode shape appears to be lateral movement of the wall hanging assembly and corresponds to 4.54 Hz. I can probably eliminate this mode since there is cross-bracing between the wall assemblies that I haven't modeled. The second mode shape is vertical movement of the entire stair assembly at 4.93 Hz. I've run to 20 modes just to see what all is happening. In those 20 there isn't a dominant "horizontal" shape, which makes sense to me since, the plates effectively tie this thing together to act like a deep beam horizontally.
Anything I'm missing here that would cause me to overestimate the frequencies?
I'm looking at a monumental stair design. The stair spans about 33' measured on the flat and has a rise of 18' total. It's one span with no opportunity for posts and is about 7' wide. I've got some relatively large HSS stringers on each end (HSS16x4). The pans will be at least 3/16" thick and will have closed risers. Strength and deflection aren't really an issue - but I'm concerned about vibrations. I used the simplified models from the new AISC DG11 for stairs but they are requiring some very large stringers.
I'm trying to capture the actual (or reasonably close) frequencies for this in RISA. Short of modelling every pan, I've done the following:
1. I've modeled flat plates between the stringers to capture the deep beam action for horizontal sway.
2. I've modeled small L3x3 angles between the stringers at intermittent locations matching the plate nodes. I can run the model without these but I get a lot of local mode shapes for the plates themselves. I consider these extraneous to what I'm doing. The angles modeled basically eliminate these modes and I feel this is reasonably accurate because I'll have a closed riser and pan assembly that creates an angle anyways. Although my modeled angles aren't as often as I'd have risers.
3. As a design note, there are HSS tubes hanging from the stringers to carry a wall. I've modeled these because I feel, if detailed properly, these will help stiffen the stringer for vertical movement - think some vierendeel truss action.
The first mode shape appears to be lateral movement of the wall hanging assembly and corresponds to 4.54 Hz. I can probably eliminate this mode since there is cross-bracing between the wall assemblies that I haven't modeled. The second mode shape is vertical movement of the entire stair assembly at 4.93 Hz. I've run to 20 modes just to see what all is happening. In those 20 there isn't a dominant "horizontal" shape, which makes sense to me since, the plates effectively tie this thing together to act like a deep beam horizontally.
Anything I'm missing here that would cause me to overestimate the frequencies?
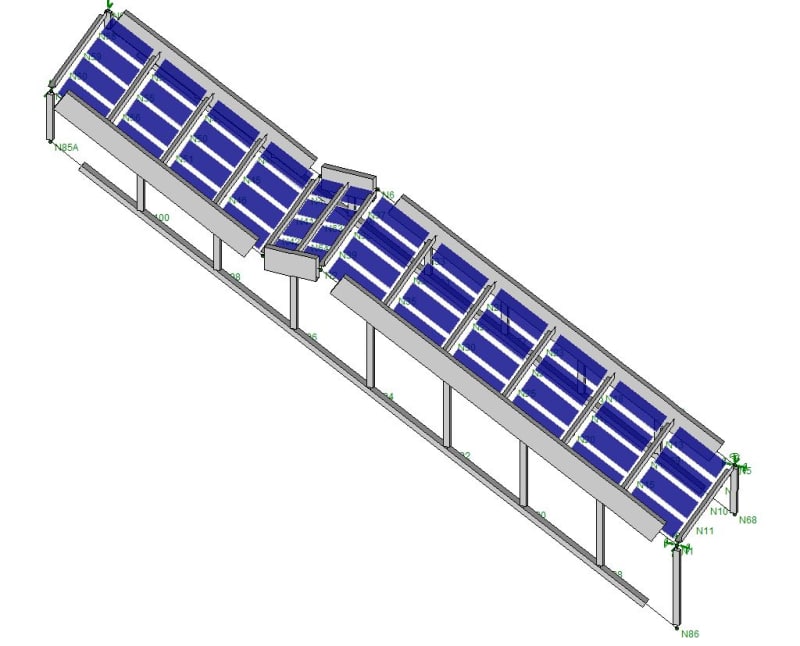
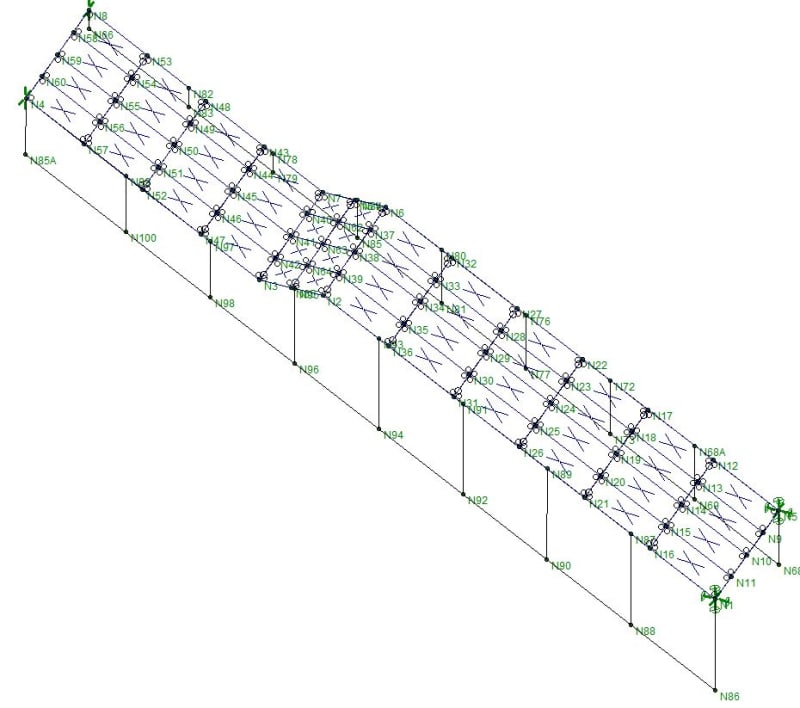