bugbus
Structural
- Aug 14, 2018
- 533
Hey folks,
I originally considered putting this topic in the Bridges forum, but I figured there's probably just as much experience with trusses in the main Structural forum.
Recently I have been working on some concept designs for steel truss pedestrian bridges with spans in the order of 20-40m (65~130 ft). These will be fabricated from square or rectangular SSHS with all the joints welded (typical T-, N- and K-joints). The top chords would be laterally unsupported (i.e. these would be half-through trusses with no sway bracing).
A couple of additional particulars: decking typically FRP mesh panels; clear width of walkway around 2-3m (6~10 ft); live load is 4 kPa (~80 psf).
I was wondering if anyone has any insights as to the most 'efficient' form of such a truss?
Specifically I'm referring to factors like:
*Minimising overall quantity/weight of SSHS required
*Minimising fabrication costs
*Most effective span/depth ratio
*Constant depth vs variable depth (is there a certain span beyond which it would be more economical to consider curving the top chord)?
A few articles on the internet I found seem to narrow it down to either the Warren or Pratt truss (below for reference). My first instinct is that overall the cost and material saving of one vs the other would be pretty minor in the grand scheme of things. But would be great to hear some of your experiences.
Thanks in advance for the responses
I originally considered putting this topic in the Bridges forum, but I figured there's probably just as much experience with trusses in the main Structural forum.
Recently I have been working on some concept designs for steel truss pedestrian bridges with spans in the order of 20-40m (65~130 ft). These will be fabricated from square or rectangular SSHS with all the joints welded (typical T-, N- and K-joints). The top chords would be laterally unsupported (i.e. these would be half-through trusses with no sway bracing).
A couple of additional particulars: decking typically FRP mesh panels; clear width of walkway around 2-3m (6~10 ft); live load is 4 kPa (~80 psf).
I was wondering if anyone has any insights as to the most 'efficient' form of such a truss?
Specifically I'm referring to factors like:
*Minimising overall quantity/weight of SSHS required
*Minimising fabrication costs
*Most effective span/depth ratio
*Constant depth vs variable depth (is there a certain span beyond which it would be more economical to consider curving the top chord)?
A few articles on the internet I found seem to narrow it down to either the Warren or Pratt truss (below for reference). My first instinct is that overall the cost and material saving of one vs the other would be pretty minor in the grand scheme of things. But would be great to hear some of your experiences.
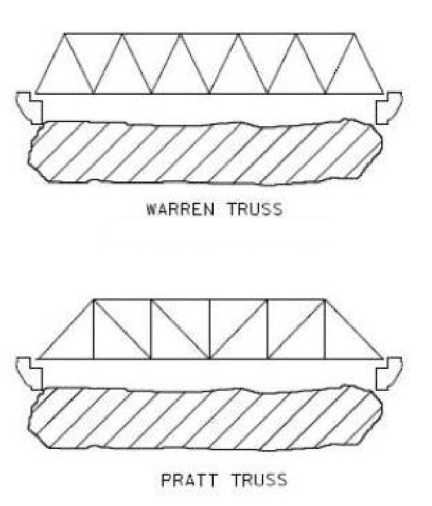
Thanks in advance for the responses