Hello,
I have a basic question regarding modeling composite laminates using MSC Patran. I need to edit input deck files that I receive from my colleagues and I use MSC Patran to do the same. I use the PCOMP editor and I have asked this question to our MSC seller as well but I am not convinced by their response.
Ref to image below, which side in Patran PCOMP editor represents bottom layup & which top? We may need to play around with some asymmetric layups and thus top & bottom side becomes important.
Second question I have is with natural frequency. If I am trying to clear the natural frequency of a structure from the frequency of a rotating source, how do I decide the range (min & max of rotating source frequency)? Any thumb rules or sources which I can find such information.
I have a basic question regarding modeling composite laminates using MSC Patran. I need to edit input deck files that I receive from my colleagues and I use MSC Patran to do the same. I use the PCOMP editor and I have asked this question to our MSC seller as well but I am not convinced by their response.
Ref to image below, which side in Patran PCOMP editor represents bottom layup & which top? We may need to play around with some asymmetric layups and thus top & bottom side becomes important.
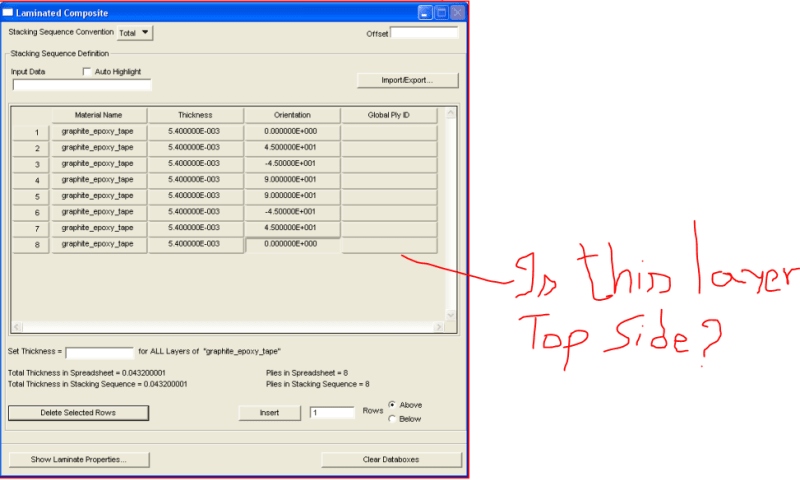
Second question I have is with natural frequency. If I am trying to clear the natural frequency of a structure from the frequency of a rotating source, how do I decide the range (min & max of rotating source frequency)? Any thumb rules or sources which I can find such information.