xlumax
Mechanical
- Jul 22, 2024
- 7
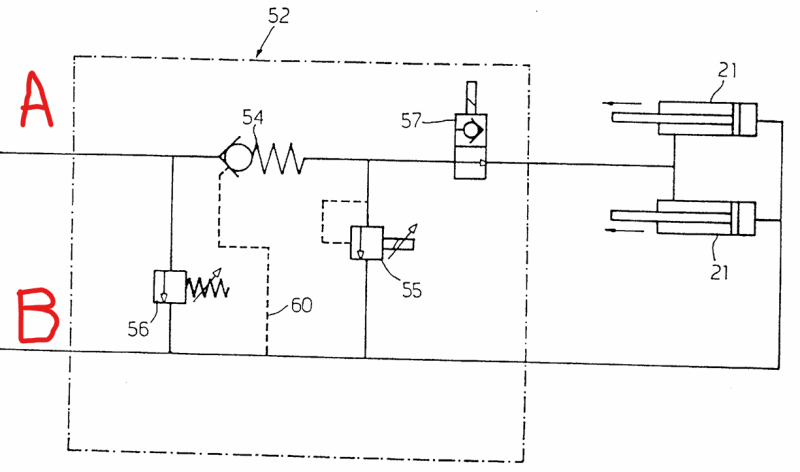
Hello everyone,
the circuit in the picture have port A and B closed (no fluidi can pass through them) and the actuators are pulled by an external force.
The pressure at A will increase until the relief valve opens up (number 55).
Can the cylinder extend?
My opinion is that it can't move if port B is not connected to tank for example.