DoubleStud
Structural
- Jul 6, 2022
- 491
What do you guys typically like to do if you are doing a new patio roof? So you have a ridge beam and two shoulder beams. Do you nest these beams inside the wall on a studpack all the way to the foundation with king stud each side? Or do you install a full studpack in the wall and connect the beam to the studpack using some kind of a hanger?
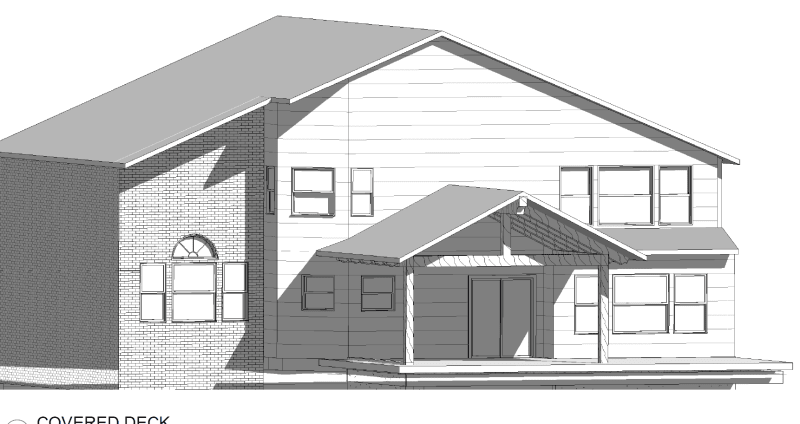