ManifestDestiny
Automotive
Hi folks
I'm relatively new to GD&T (and even drawing) but after wanting to learn it for quite some time, and have taken a gentler approach of using for a personal project before I feel comfortable using it professionally (early career - so baby steps).
I've probably jumped in the deep end with a part that is trickier than most to dimension, so I've resolved to using the first sheet for the overall geometry and the second sheet to position holes. These are by no means a final draft, but they at least show the direction I'm going in.
On the first sheet I'm unsure if I've dimensioned the angles on the triangular shape well enough to fully define the geometry. I'm trying to keep it as simple as possible and avoid redundant dimensions, but I'm not sure if I need more information, or if my approach is completely wrong here. I'm also unsure how linear dimensions come off a fillet edge (111mm length in the Top view).
On the second sheet I've used control frames a bit more extensively to define hole positions. I just realized that I don't need a section view when a wireframe could have sufficed as well.
Ignore most tolerances as I'm yet to fully specify that based on what the shop is capable of.
Any advice/criticism appreciated!
I'm relatively new to GD&T (and even drawing) but after wanting to learn it for quite some time, and have taken a gentler approach of using for a personal project before I feel comfortable using it professionally (early career - so baby steps).
I've probably jumped in the deep end with a part that is trickier than most to dimension, so I've resolved to using the first sheet for the overall geometry and the second sheet to position holes. These are by no means a final draft, but they at least show the direction I'm going in.
On the first sheet I'm unsure if I've dimensioned the angles on the triangular shape well enough to fully define the geometry. I'm trying to keep it as simple as possible and avoid redundant dimensions, but I'm not sure if I need more information, or if my approach is completely wrong here. I'm also unsure how linear dimensions come off a fillet edge (111mm length in the Top view).
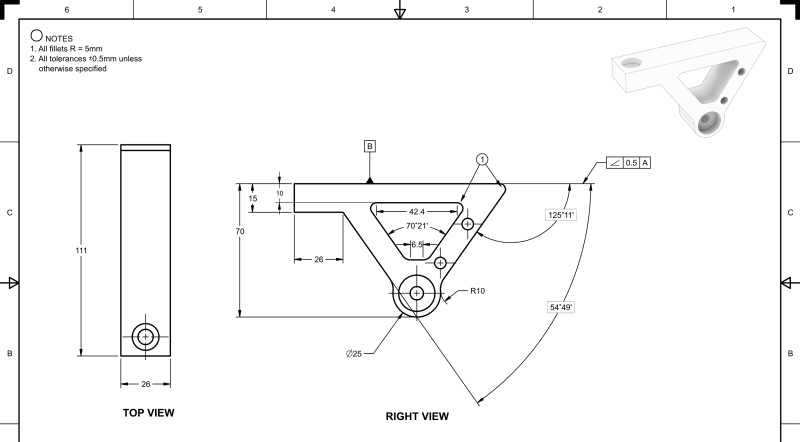
On the second sheet I've used control frames a bit more extensively to define hole positions. I just realized that I don't need a section view when a wireframe could have sufficed as well.
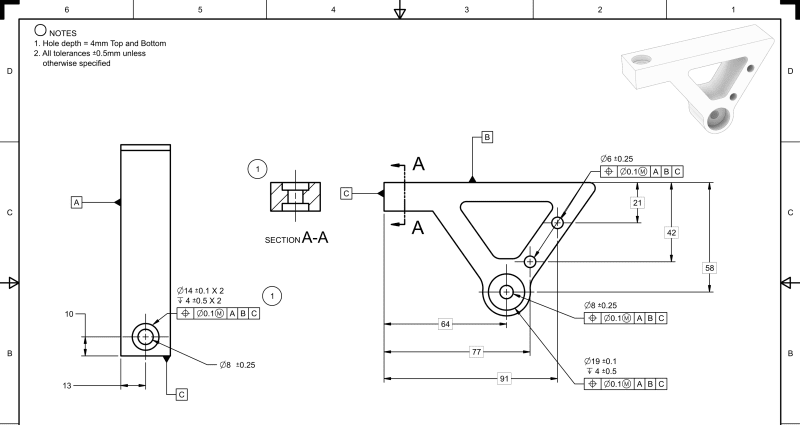
Ignore most tolerances as I'm yet to fully specify that based on what the shop is capable of.
Any advice/criticism appreciated!