I'm tasked with designing a wacko Nixie Tube clock. I have to use the IN-28 which is a Soviet era tube that is just a single bright dot about an inch in diameter.
Here's the pertinent data sheet page:
Normally one hooks the B+ voltage to a Nixie's Anode (a metal screen) and each of the digits is a cathode that gets grounded to light it.
Well-and-fine, but this particular tube sports a Grid pin too. See pin 1 - Cetka. Cetka means 'Grid'.
Any of you tube-heads know what I should do with it? Do I ignore it?
Pins 2, 5, and 6 are NO-CONNECTION.
3 and 7 are ANODES
4 is the CATHODE
I'd be nice if anyone also knew if the diagram was viewed from below or above too. The tube is hard to see into since the sides are pretty obscured.
Keith Cress
kcress -
Here's the pertinent data sheet page:
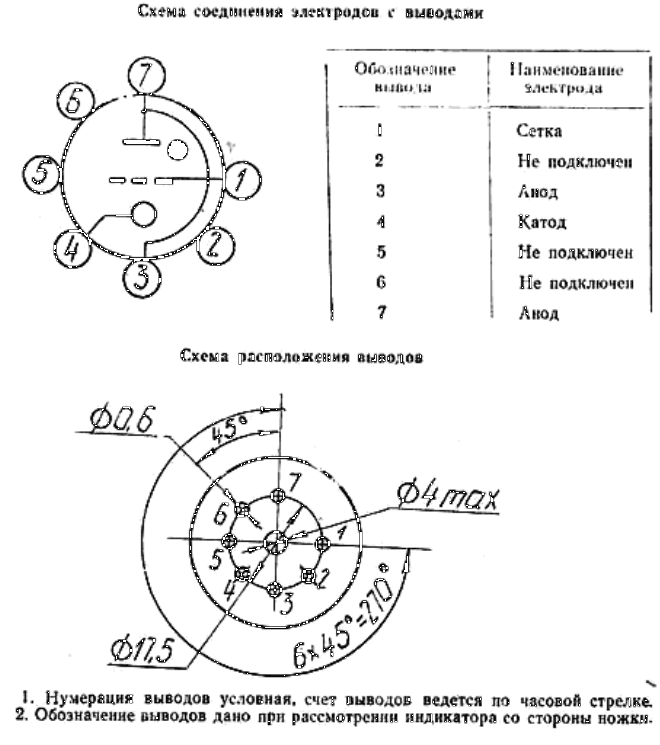
Normally one hooks the B+ voltage to a Nixie's Anode (a metal screen) and each of the digits is a cathode that gets grounded to light it.
Well-and-fine, but this particular tube sports a Grid pin too. See pin 1 - Cetka. Cetka means 'Grid'.
Any of you tube-heads know what I should do with it? Do I ignore it?
Pins 2, 5, and 6 are NO-CONNECTION.
3 and 7 are ANODES
4 is the CATHODE
I'd be nice if anyone also knew if the diagram was viewed from below or above too. The tube is hard to see into since the sides are pretty obscured.
Keith Cress
kcress -