RFreund
Structural
- Aug 14, 2010
- 1,885
I've been seeing this more and more recently where the EOR is specifying that the non-loadbearing CFM wall system be used as a shearwall (either strapped or sheathed) to resist lateral loads.
In concept, I like the idea. There is a wall there, why not use it? However, when you get into the details, it gets hard to justify all the eccentricities involved. How do you put lateral loads into the wall and not gravity loads and resolve all the eccentricities?I'm posting this, hoping that someone comes to the defense of this system. I will try to defend it...
After posting this, I think I'm a believer. The eccentricities are resolved and for single story buildings of relatively short heights, I'd be ok with it. So this started as a rant/problem, but has turned into more of a PSA (too much effort not to post at this point). But I'm open to other ideas and input.
Problems common to both:
If you sheath or strap the outside (which is typically shown like that in the EOR drawing) you have to deal with the eccentricity across the wall thickness. This might be ok, because there is already eccentricity in these types of walls when you only sheath or strap one side. Many engineers forget this when designing strap walls, but you should account for this by applying a moment to your chord studs equal to wall thickness/2 * the strap force.
Situation-1 : No cantilever parapet.
In plane loads are resisted by a slotted connection to a heavy gauge track. Out of plane loads are handled by another slotted clip angle directly connected to the stud.
Situation-2 : Cantilever parapet.
This is a little tougher because you need to add a bunch of blocking. It is probably best to sheath this wall as opposed to using straps. In plane loads are resisted by a slotted connection to a heavy gauge blocking. If a strapped shear wall used, then you need to transfer compression through this blocking. Out of plane loads are handled by another slotted clip angle directly connected to the stud.
In concept, I like the idea. There is a wall there, why not use it? However, when you get into the details, it gets hard to justify all the eccentricities involved. How do you put lateral loads into the wall and not gravity loads and resolve all the eccentricities?
After posting this, I think I'm a believer. The eccentricities are resolved and for single story buildings of relatively short heights, I'd be ok with it. So this started as a rant/problem, but has turned into more of a PSA (too much effort not to post at this point). But I'm open to other ideas and input.
Problems common to both:
If you sheath or strap the outside (which is typically shown like that in the EOR drawing) you have to deal with the eccentricity across the wall thickness. This might be ok, because there is already eccentricity in these types of walls when you only sheath or strap one side. Many engineers forget this when designing strap walls, but you should account for this by applying a moment to your chord studs equal to wall thickness/2 * the strap force.
Situation-1 : No cantilever parapet.
In plane loads are resisted by a slotted connection to a heavy gauge track. Out of plane loads are handled by another slotted clip angle directly connected to the stud.
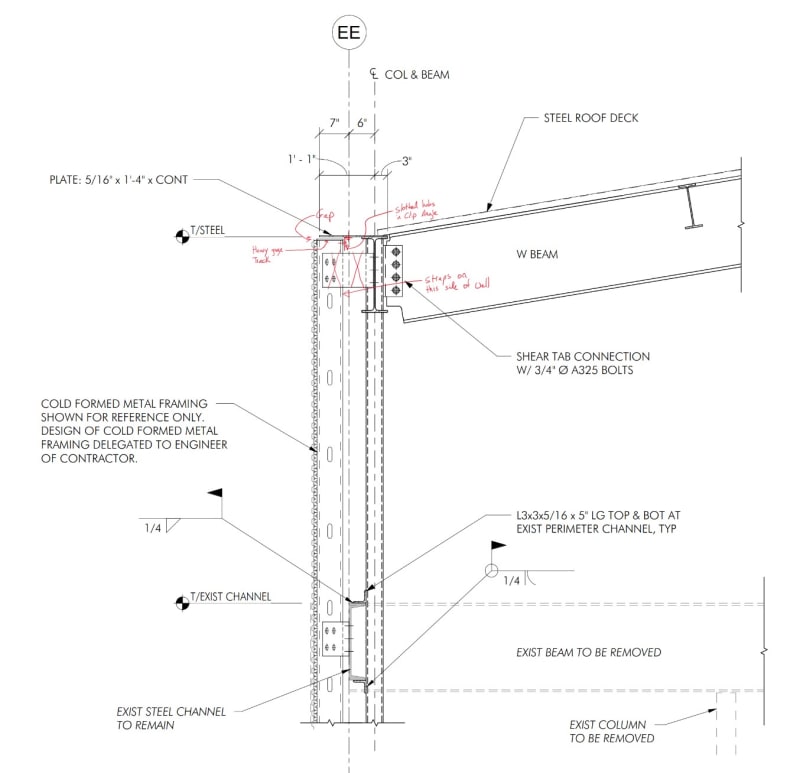
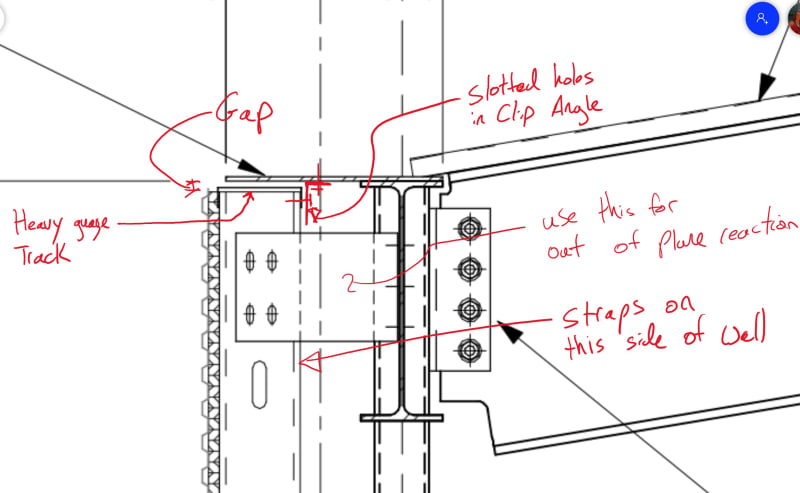
Situation-2 : Cantilever parapet.
This is a little tougher because you need to add a bunch of blocking. It is probably best to sheath this wall as opposed to using straps. In plane loads are resisted by a slotted connection to a heavy gauge blocking. If a strapped shear wall used, then you need to transfer compression through this blocking. Out of plane loads are handled by another slotted clip angle directly connected to the stud.
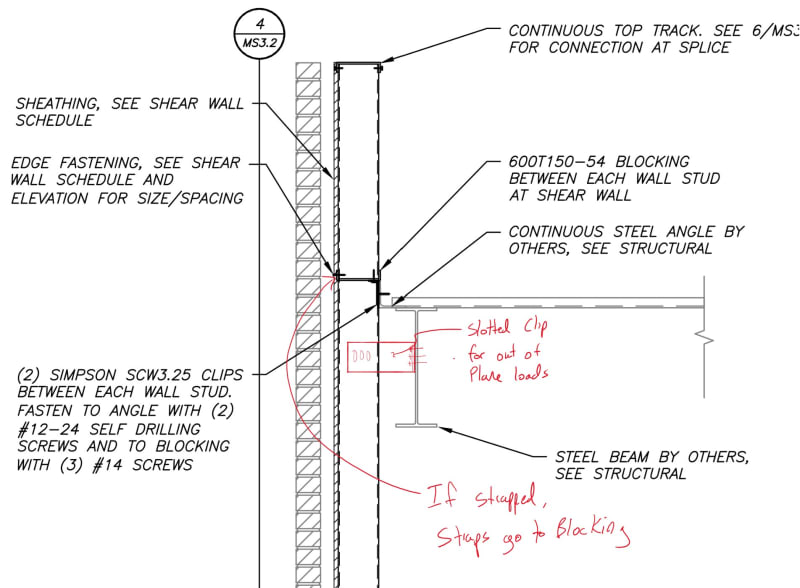
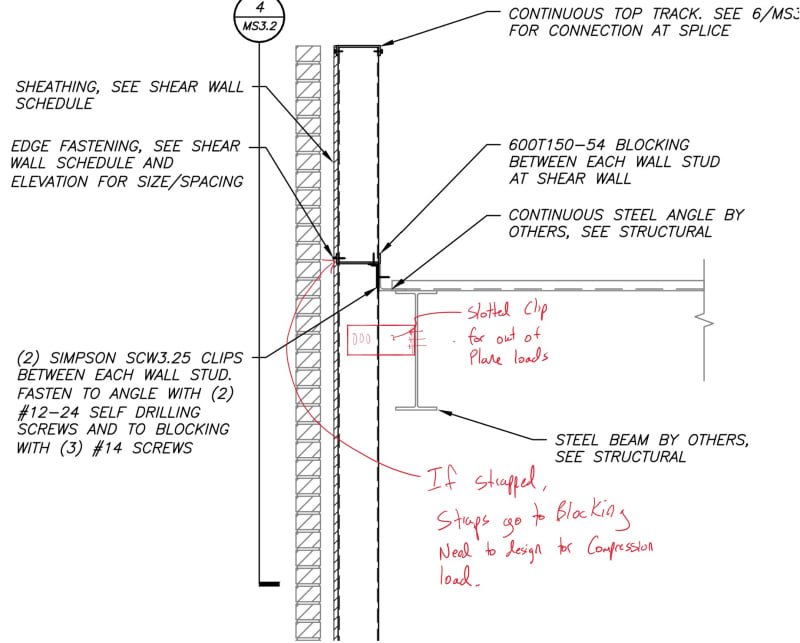