men8th
Nuclear
- Jul 1, 2016
- 21
We are in the process of designing a large heat exchanger. It has two fixed tubesheets, for example TEMA type AEL. The tubesheets are "loose" and sandwiched between girth flanges on the shell and channel, similar to the image below.
The nozzle loads on the channel are considerable and the nozzles are oblique (hillside). When the nozzle loads are resolved around the centroid of the girth flange bolt group there is a moment which will attempt to rotate the channel about its axis.
As things stand, there is nothing to react the moment which is rotating the channel apart from the friction in the joint between the channel, tubesheet and shell. If the friction fails, the studbolts which attach the channel to the shell across the girth flange will be put in shear by the moment which is spinning the channel about its axis. Having fasteners in shear is not good design, and we do not want to be reliant on friction.
Has anyone come across this problem before, and are there any good design details which could be suggested. Obviously it would be possible to key or pin the girth flanges and tubesheets. I do not anticipate that the channel will ever be removed once the unit is in service. (Cover will be removed to inspect tube-side from time to time.)
Things we cannot do:
[ul]
[li]Weld the tubesheets to the channel or shell (materials problems)[/li]
[li]Change from two fixed tubesheets (client stipulation)[/li]
[li]Reduce the nozzle loads (constrained by other pipe layout issues)[/li]
[/ul]
Looking forward to a flood of good ideas!
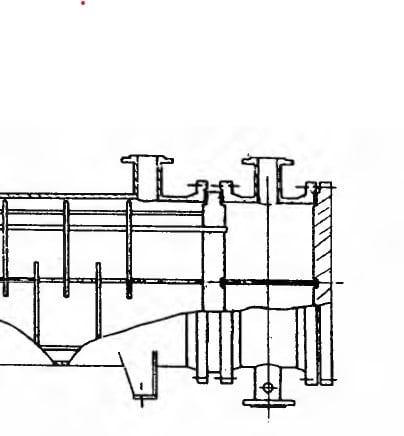
The nozzle loads on the channel are considerable and the nozzles are oblique (hillside). When the nozzle loads are resolved around the centroid of the girth flange bolt group there is a moment which will attempt to rotate the channel about its axis.
As things stand, there is nothing to react the moment which is rotating the channel apart from the friction in the joint between the channel, tubesheet and shell. If the friction fails, the studbolts which attach the channel to the shell across the girth flange will be put in shear by the moment which is spinning the channel about its axis. Having fasteners in shear is not good design, and we do not want to be reliant on friction.
Has anyone come across this problem before, and are there any good design details which could be suggested. Obviously it would be possible to key or pin the girth flanges and tubesheets. I do not anticipate that the channel will ever be removed once the unit is in service. (Cover will be removed to inspect tube-side from time to time.)
Things we cannot do:
[ul]
[li]Weld the tubesheets to the channel or shell (materials problems)[/li]
[li]Change from two fixed tubesheets (client stipulation)[/li]
[li]Reduce the nozzle loads (constrained by other pipe layout issues)[/li]
[/ul]
Looking forward to a flood of good ideas!