NXerGeneration
Automotive
Hello,
Can somebody take a look at it and let me know what am I missing here? See attached.
I'm just getting into the Basic NX10 Design Simulation and I have set up a simple load case where a plunger slides into the rotating pin attached to a fixed bracket. The goal was to see what forces get transferred into the bracket but no matter what I try I get a reaction on the pin and plunger but the bracket stays cold. See attached.
Can somebody take a look at it and let me know what am I missing here? See attached.
I'm just getting into the Basic NX10 Design Simulation and I have set up a simple load case where a plunger slides into the rotating pin attached to a fixed bracket. The goal was to see what forces get transferred into the bracket but no matter what I try I get a reaction on the pin and plunger but the bracket stays cold. See attached.
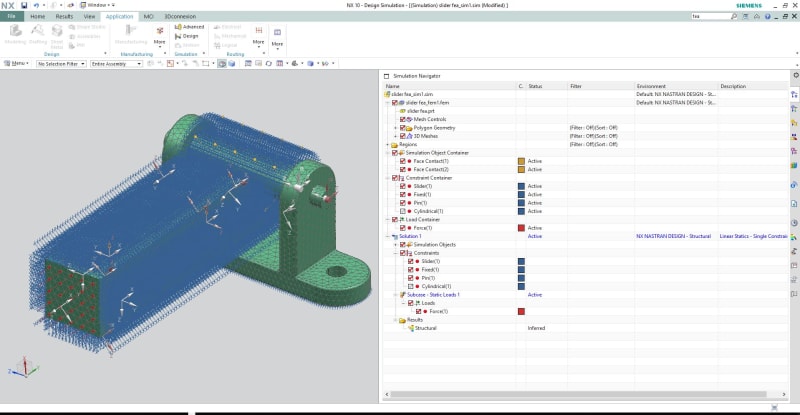
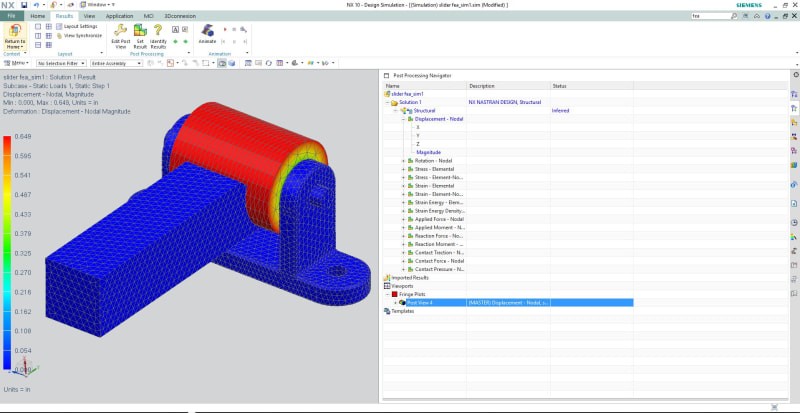