aniiben
Mechanical
- May 9, 2017
- 158
Based on your individual experience, does anyone know if a gland groove detail should be
defined with GD&T?
All catalogs found online have angles with plus minus (zero degrees to 5 degrees Typ.) for the sides (groove sides) along with the groove depth and groove width.
How would you GDT this feature?
Does it really need it?
Any feedback will be appreciated (experience, training manuals, books, etc.)
defined with GD&T?
All catalogs found online have angles with plus minus (zero degrees to 5 degrees Typ.) for the sides (groove sides) along with the groove depth and groove width.
How would you GDT this feature?
Does it really need it?
Any feedback will be appreciated (experience, training manuals, books, etc.)
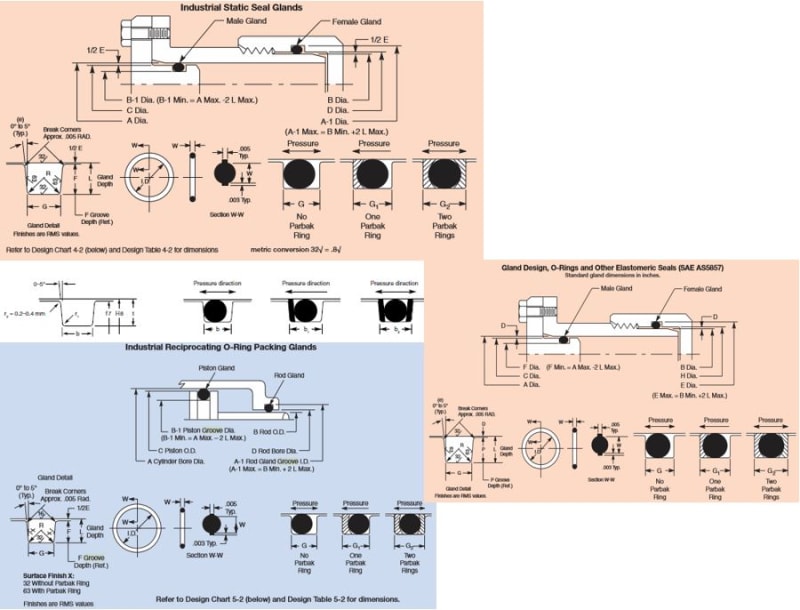