Baraa Karam
Mechanical
- Mar 7, 2022
- 21
I'm working on some sort of enclosure, I have some limitation in the overall size of the enclosure, and I'm wondering if there is some guideline for the width "T" of the face next to the o-ring groove (as shown in the attached picture). the enclosure's material is Al.
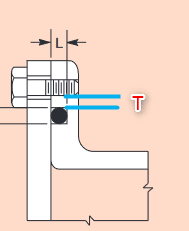