Skatemav86
Mechanical
- Jul 14, 2020
- 8
Hi all,
I have a problem when trying to seal the pressurized casing in the image below.
Initially, I have thought about 2 axial o-rings and 2 longitudinal o-rings (as shown), but I don't know how to avoid possible leakage at the o-ring interfaces.
The fluid is cyclopentane at 260 °C.
Do you know how to overcome this issue?
Thank you in advance.
Fede
I have a problem when trying to seal the pressurized casing in the image below.
Initially, I have thought about 2 axial o-rings and 2 longitudinal o-rings (as shown), but I don't know how to avoid possible leakage at the o-ring interfaces.
The fluid is cyclopentane at 260 °C.
Do you know how to overcome this issue?
Thank you in advance.
Fede
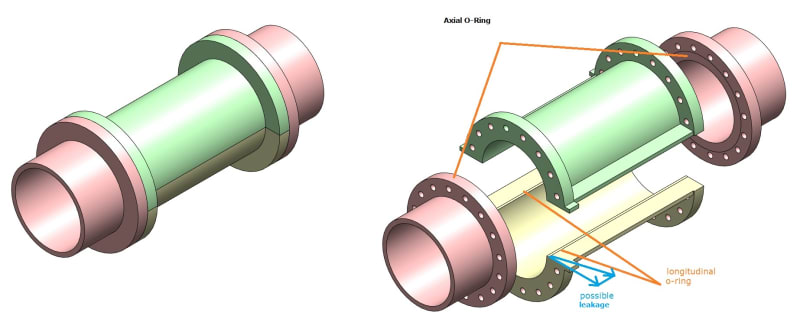