sendithard
Industrial
I'm making my way thru the standard to cement it all and the below pic raised my eyebrow.
Since the keyway locks the mutually perpendicular planes in rotation, and it has an offsetting basic dimension, they are saying the keyway UAME(unrelated actual mating envelope) must be set at this distance AS WELL a maintain a parallel relationship to one of the planes.
Does this mean if the keyway was actually made 5 degrees off angle(and this wasn't properly controlled) that when you set up the UAME it must be in reality or in theory placed into the keyway parallel to said plane, which would mean it may only go in 20% of the depth due to the poor angularity?
Since the keyway locks the mutually perpendicular planes in rotation, and it has an offsetting basic dimension, they are saying the keyway UAME(unrelated actual mating envelope) must be set at this distance AS WELL a maintain a parallel relationship to one of the planes.
Does this mean if the keyway was actually made 5 degrees off angle(and this wasn't properly controlled) that when you set up the UAME it must be in reality or in theory placed into the keyway parallel to said plane, which would mean it may only go in 20% of the depth due to the poor angularity?
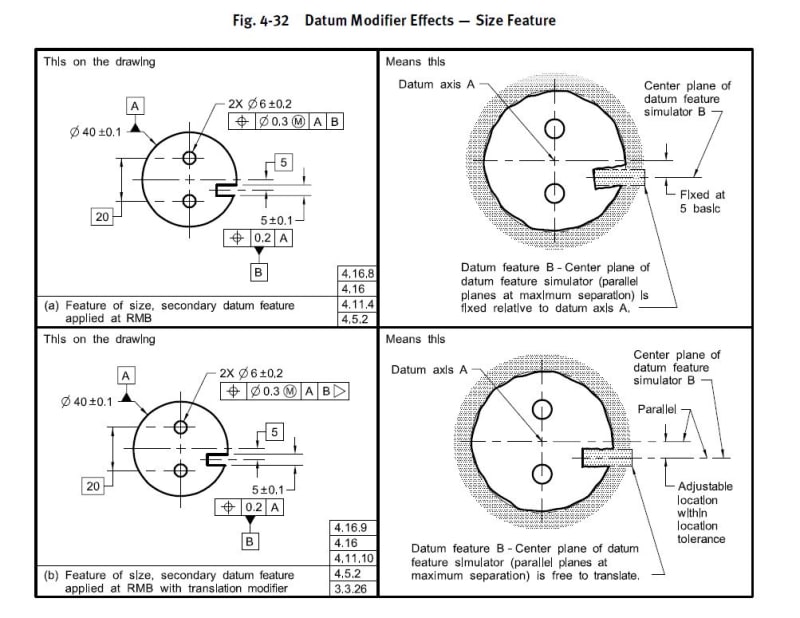