82ghost82
Chemical
- Oct 7, 2007
- 10
Hi community,
I am the developer of an equipment similar to a pump.
This equipment has a bearing lantern with 2 bearings: 1 radial deep groove single row ball bearing (bearing 1) and 1 angular contact deep groove double row bearing (bearing 2).
Bearing data:
Bearing 1:
Internal diameter: 45 mm (about 1,77 inches)
External diameter: 85 mm (about 3,34 inches)
Bearing 2:
Internal diameter: 45 mm (about 1,77 inches)
External diameter: 85 mm (about 3,34 inches)
The shaft rotates at 2960 rpm.
Bearings are cooled and lubricated with a static oil sump (no recirculation, no cooling, no mist, no oil rings or flinger disc).
This should be ok as DN is 1,77x2960 = 5221 < 6000 (literature data).
The bearing lantern contains 1 liter of oil, with its free surface reaching the half of the 6 o' clock ball of the bearing.
This is my first equipment with a bearing lantern, so I have no real data about temperatures that the bearings could reach.
From literature I found different data, the most reliable declare that I should expect a temperature of the outer ring of no more than 50-55 °C + ambient temperature.
Experimental data found on scientific articles state a temperature of 90 °C for a 65 mm bearing rotating at 3600 rpm.
Based on these data I think I can expect a temperature of about 80-85 °C in stationary state for the outer ring (with the bulk of the oil at 70-75 °C).
Now I have to choose a right oil to lubricate and cool the bearings: I know there are mineral and synthetic oils, with latter being superior because their higher IV and stability.
I also know that the right oil is an important parameter: low viscosity oils will not create enough film and friction of the balls with the rings will make the temperature rise and maybe damage the bearing.
Too high viscosity oil will not lubricate properly, with the same effects.
I looked at different charts for viscosity/temperatures/type of oils.
For mineral oils I found that, at the operating temperature, a proper viscosity should be around 20 cSt.
With these data an ISO VG 68 mineral oil should work.
However, I don't want to use mineral oils, as I want the best for my equipment, so my choice would be a premium synthetic oil (PAO based).
The Mobil SHC 600 series seems it's what I need.
So, searching for synthetic oils, I found an interesting article written by Prof. Bloch, which is available for free here:
These are the most important sentences in the article:
1- premium grade synthetic VG 32 is the "protection-equivalent" of mineral oil VG 68
2- Specifically, the results of the entire study established that ISO Grade 68 mineral lubricating fluids are equal in terms of oil film thickness and tenacity to ISO Grade 32 synthetic oils.
3- the substitution of ISO Grade 32 synthetic lubricants for ISO Grade 68 mineral oils in a refinery or petrochemical plant is both feasible and recommended. Such substitutions will not incur in the risk of increasing the frequency of in-service bearing failures.
4- Operating a 65 mm bearing at 3600 rpm with even a high-quality synthetic lubricant (PAO-base, ISO Grade 32; Urbiola Soto, 2002) reaching the center of the lowest bearing ball caused oil temperatures to exceed 75°C (167°F). Bearing outer ring temperatures hovered around 90°C (194°F).
5- synthetic ISO Grade 32 viscosity lubricants produce measurably lower frictional energy losses than quality mineral oils with the same functionally equivalent ISO grade 68 viscosity. Functional equivalency would be established by the same film thickness and degree of bearing protection achieved by the two different lubricants.
6- Premium-grade ISO VG 32 synthetics serve both rolling element and sleeve bearings. Although ISO VG 68 synthetics could be used for rolling element bearings, synthetic VG 32 lubricants will provide adequate lubrication and minimize frictional energy consumed for all except high temperature services.
Based on these statements I would choose for my equipment the Mobil SHC 624, which is a PAO based synthetic oil, ISO VG 32.
Mobil SHC 624 data:
cTs at 40 °C: 32
cTs at 100 °C: 6,3
Viscosity of this oil at 75 °C should be around 11 cTs, decreasing to less than 10 cTs at 80 °C...
This chart suggest a minimum of 11 cTs for my application (but again this chart is based on mineral oils): dm=65mm, rpm=2960
For Prof. Bloch the synthetic VG 32 should be ok...
What do you think about?
I am the developer of an equipment similar to a pump.
This equipment has a bearing lantern with 2 bearings: 1 radial deep groove single row ball bearing (bearing 1) and 1 angular contact deep groove double row bearing (bearing 2).
Bearing data:
Bearing 1:
Internal diameter: 45 mm (about 1,77 inches)
External diameter: 85 mm (about 3,34 inches)
Bearing 2:
Internal diameter: 45 mm (about 1,77 inches)
External diameter: 85 mm (about 3,34 inches)
The shaft rotates at 2960 rpm.
Bearings are cooled and lubricated with a static oil sump (no recirculation, no cooling, no mist, no oil rings or flinger disc).
This should be ok as DN is 1,77x2960 = 5221 < 6000 (literature data).
The bearing lantern contains 1 liter of oil, with its free surface reaching the half of the 6 o' clock ball of the bearing.
This is my first equipment with a bearing lantern, so I have no real data about temperatures that the bearings could reach.
From literature I found different data, the most reliable declare that I should expect a temperature of the outer ring of no more than 50-55 °C + ambient temperature.
Experimental data found on scientific articles state a temperature of 90 °C for a 65 mm bearing rotating at 3600 rpm.
Based on these data I think I can expect a temperature of about 80-85 °C in stationary state for the outer ring (with the bulk of the oil at 70-75 °C).
Now I have to choose a right oil to lubricate and cool the bearings: I know there are mineral and synthetic oils, with latter being superior because their higher IV and stability.
I also know that the right oil is an important parameter: low viscosity oils will not create enough film and friction of the balls with the rings will make the temperature rise and maybe damage the bearing.
Too high viscosity oil will not lubricate properly, with the same effects.
I looked at different charts for viscosity/temperatures/type of oils.
For mineral oils I found that, at the operating temperature, a proper viscosity should be around 20 cSt.
With these data an ISO VG 68 mineral oil should work.
However, I don't want to use mineral oils, as I want the best for my equipment, so my choice would be a premium synthetic oil (PAO based).
The Mobil SHC 600 series seems it's what I need.
So, searching for synthetic oils, I found an interesting article written by Prof. Bloch, which is available for free here:
These are the most important sentences in the article:
1- premium grade synthetic VG 32 is the "protection-equivalent" of mineral oil VG 68
2- Specifically, the results of the entire study established that ISO Grade 68 mineral lubricating fluids are equal in terms of oil film thickness and tenacity to ISO Grade 32 synthetic oils.
3- the substitution of ISO Grade 32 synthetic lubricants for ISO Grade 68 mineral oils in a refinery or petrochemical plant is both feasible and recommended. Such substitutions will not incur in the risk of increasing the frequency of in-service bearing failures.
4- Operating a 65 mm bearing at 3600 rpm with even a high-quality synthetic lubricant (PAO-base, ISO Grade 32; Urbiola Soto, 2002) reaching the center of the lowest bearing ball caused oil temperatures to exceed 75°C (167°F). Bearing outer ring temperatures hovered around 90°C (194°F).
5- synthetic ISO Grade 32 viscosity lubricants produce measurably lower frictional energy losses than quality mineral oils with the same functionally equivalent ISO grade 68 viscosity. Functional equivalency would be established by the same film thickness and degree of bearing protection achieved by the two different lubricants.
6- Premium-grade ISO VG 32 synthetics serve both rolling element and sleeve bearings. Although ISO VG 68 synthetics could be used for rolling element bearings, synthetic VG 32 lubricants will provide adequate lubrication and minimize frictional energy consumed for all except high temperature services.
Based on these statements I would choose for my equipment the Mobil SHC 624, which is a PAO based synthetic oil, ISO VG 32.
Mobil SHC 624 data:
cTs at 40 °C: 32
cTs at 100 °C: 6,3
Viscosity of this oil at 75 °C should be around 11 cTs, decreasing to less than 10 cTs at 80 °C...
This chart suggest a minimum of 11 cTs for my application (but again this chart is based on mineral oils): dm=65mm, rpm=2960
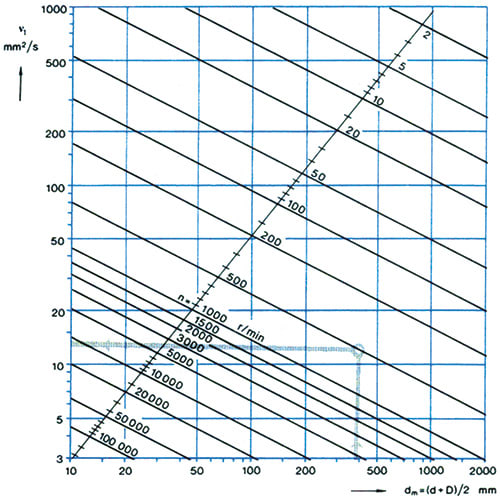
For Prof. Bloch the synthetic VG 32 should be ok...
What do you think about?