joji90
Petroleum
- Jun 26, 2016
- 22
Dear members,
I have a XCV( fail open) and has to be slow opening , the idea is to demolish the old valve and install new one., but when I see the pneumatic hookup of the old valve, I don't understand it, I made a pneumatic drawing from the existing setup but could identify the clouded component and hence couldn't understand the working of the valve. can anyone help please?
Also please check the PDF doc in attatchment for additional info.
I have a XCV( fail open) and has to be slow opening , the idea is to demolish the old valve and install new one., but when I see the pneumatic hookup of the old valve, I don't understand it, I made a pneumatic drawing from the existing setup but could identify the clouded component and hence couldn't understand the working of the valve. can anyone help please?
Also please check the PDF doc in attatchment for additional info.
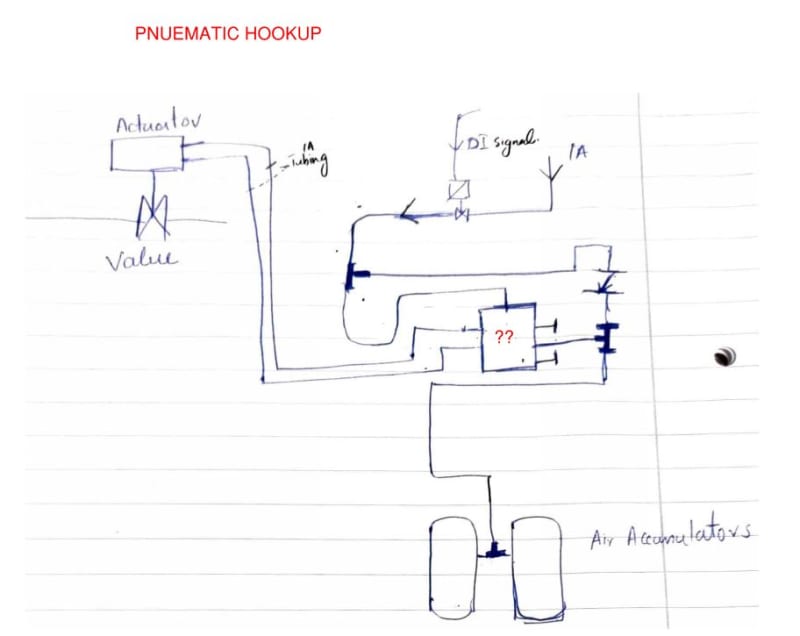