I have a Centrifugal Pump designed for about 12m3/hr (from purchase information with the supplier). The pump curve is without efficiency lines and as follows:
We are however, running the pump at only 3.5 m3/hr maximum, which based on the above, means it's not even on the curve. Although I don't have the BEP, but based on the rated 12m3/hr, this means it's about only 30% or less.
This is obviously not ideal and may lead to chronic failures of parts like seals, bearing, etc. The seal has actually failed twice (leak) in the last 2 years. Apart from changing to a new pump altogether, what are the cheaper options to solve this?
a) Install a recirculation line at the pump to increase the flow at the pump? Comments?
b) Reduce the pump speed by installing a variable speed drive?? Comments??
c) What else?
---engineering your life---
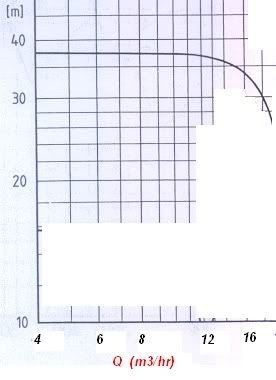
We are however, running the pump at only 3.5 m3/hr maximum, which based on the above, means it's not even on the curve. Although I don't have the BEP, but based on the rated 12m3/hr, this means it's about only 30% or less.
This is obviously not ideal and may lead to chronic failures of parts like seals, bearing, etc. The seal has actually failed twice (leak) in the last 2 years. Apart from changing to a new pump altogether, what are the cheaper options to solve this?
a) Install a recirculation line at the pump to increase the flow at the pump? Comments?
b) Reduce the pump speed by installing a variable speed drive?? Comments??
c) What else?
---engineering your life---