Ben29
Structural
- Aug 7, 2014
- 324
I am designing the foundations for a PEMB. The building will have a full basement and the PEMB columns will sit on pedestals. The column baseplate will be elevated to the first floor elevation. I am also designing the first floor framing. The architect originally wanted steel bar joist (non composite) floor system with a 4" thick concrete deck. But I am starting to convince myself that composite beams are the way to go.
I am trying to figure out how to brace the PEMB column base against the horizontal thrust. My thought is to have beams frame into the column pedestals via a steel plate bolted to the pedestal via epoxy anchors or CIP anchors. Is this a bad idea? Is there a better way?
I am trying to figure out how to brace the PEMB column base against the horizontal thrust. My thought is to have beams frame into the column pedestals via a steel plate bolted to the pedestal via epoxy anchors or CIP anchors. Is this a bad idea? Is there a better way?
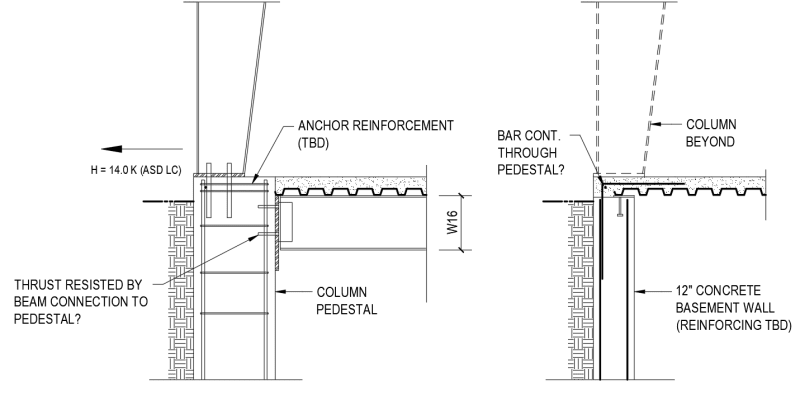