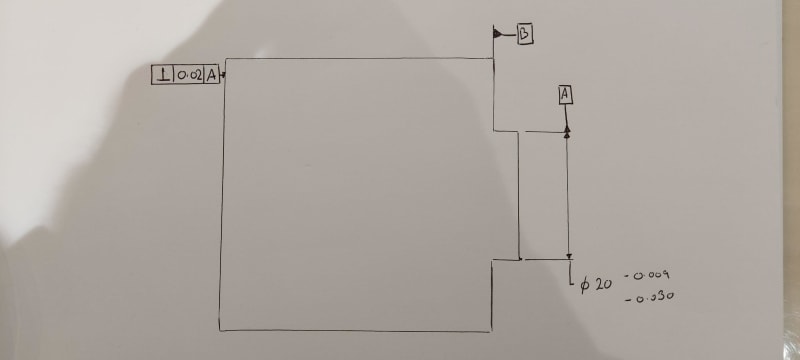
Hi
Please see attached sketch.
This is rough sketch of a perpendicular callout. In principle the perpendicular call out here is ok. The issue with measuring purposes although no sizes giving is the length of Datum A axis.
Can anyone explain why you cannot measure the plane perpendicular to B A feature control frame. Due to the axis being so small on Datum A which always causes issues either with manual measurement or with a CMM.
So one solution would be to change the callout to parallel to Datum B although I am wondering if there is another solution.
My thinking is on my CMM I can create a Cylinder which is basically an RAME. This cylinder would be perfectly perpendicular to Datum B and positionally orientated to datum A. I then can check this plane to my created Cylinder which always provides consistent results due to the fact Datum B provides stability in the measurement.
I cannot however change the drawing to suit my methodolgy as it doesn't seem valid. I am working to ASME 14.5 2018.
Does anyone have any suggestions?
Thanks
Ross