I have a part that I'm trying to have fabricated that has length with width ratio of 48:1 (see image). I'm having trouble specifying a reasonable perpendicularity because of this large aspect ratio. The grind houses say they can only hold .002"/12" flatness on datum A shown (over the 48" length). At any given location along the length (labeled 1, 2, 3, 4, n in my drawing), I really need the top surface to be perpendicular to the front surface within .001". However, I don't really care if the front of the part at location "1" is perpendicular to the top at location "n". If I call out perpendicular within .001", no fabricator can guarantee this over the 48" length of the part. Also, if I call out a perpendicularity of .003"/12" (which could work over the entire length of the part), no fabricator will guaranteed .0003" perpendicularity across the 1" width at the top of the part. I'm looking for a way to say "I need the perpendicularity to be .001" at any point along the length in the x-direction (i.e. 1, 2, 3, 4, etc), but I only need perpendicularity of .003/12 along the entire length".
Can anyone tell me how to explain this on a drawing?[URL unfurl="true"]https://res.cloudinary.com/engineering-com/image/upload/v1690569963/tips/Perpendicularity_Question_j4pbda.pdf[/url]
Can anyone tell me how to explain this on a drawing?[URL unfurl="true"]https://res.cloudinary.com/engineering-com/image/upload/v1690569963/tips/Perpendicularity_Question_j4pbda.pdf[/url]
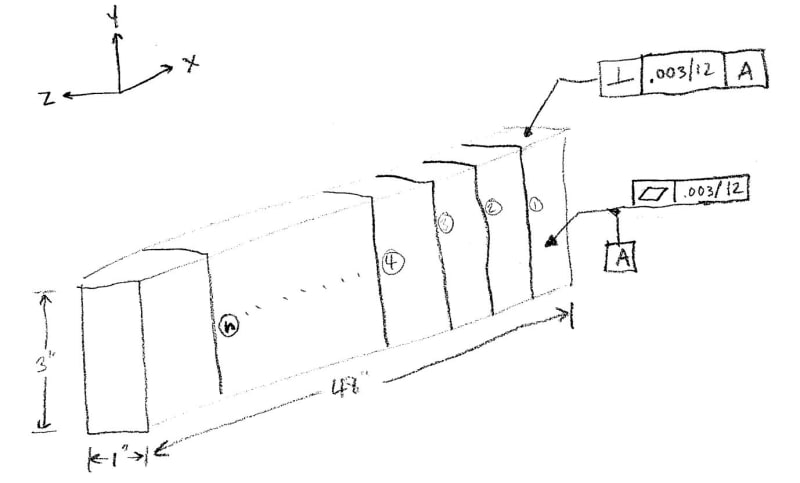