M
member 1218881
Guest
When I put the composite beams between two steel beams connected to the shear wall as seen below, the P-M-M ratios of the steel beams are high. This is the example in the first picture.
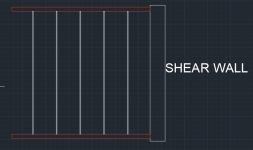
In the second picture: Connecting these beams to the walls creates the following problems. To connect steel beams to bulkheads in this way, a large number of steel plates are required. In addition, these beams are connected to the walls in a way that creates a moment on their weak axes.
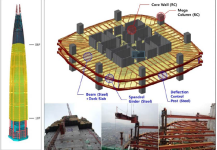
The building in the picture belongs to the Lotte Tower building. What I want to explain is how correct it is to connect composite beams to walls in this way. (I think these beams have moment transferring connections, they are not pinned)
Which method do you find more accurate?
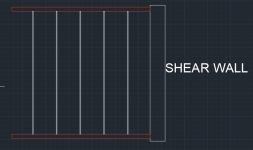
In the second picture: Connecting these beams to the walls creates the following problems. To connect steel beams to bulkheads in this way, a large number of steel plates are required. In addition, these beams are connected to the walls in a way that creates a moment on their weak axes.
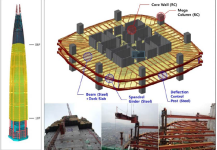
The building in the picture belongs to the Lotte Tower building. What I want to explain is how correct it is to connect composite beams to walls in this way. (I think these beams have moment transferring connections, they are not pinned)
Which method do you find more accurate?
Last edited by a moderator: