Hey everyone - I've lurked on this forum for a while, and have pulled some VERY useful information from y'all in the past, but one thing has been eluding me recently. I'm trying to recreate a spreadsheet tool I once had at a former employer that would output pipe stress for L and Z bends used for natural expansion compensation. I want to use this tool after I already have the piping layout "mostly" designed, to check where I need to add expansion compensation.
My issue: I can find in the ASHRAE books the full long form formula for L-bends that is designed to solve for the short leg if the long leg is known. I can reverse engineering this equation to solve for the "stress allowed" which becomes the "calculated stress", as I know both the long and short leg dimensions I have laid out.
Long Formula, that I can work to solve for "Sa":
It then shows a "simplified" formula for this same calculation that can NOT be reverse engineered because it assumes a reasonable "stress allowed" number to approximate the short leg that is good for carbon steel and copper piping.
Short Formula:
However, when we jump to the Z-bend section, ASHRAE only shows the simplified formula... I want the long-form equation for a Z-bend that I can reverse and solve for the stress.
Anyone happen to have a resource that shows the full long-form version of the Z bend formula?
My issue: I can find in the ASHRAE books the full long form formula for L-bends that is designed to solve for the short leg if the long leg is known. I can reverse engineering this equation to solve for the "stress allowed" which becomes the "calculated stress", as I know both the long and short leg dimensions I have laid out.
Long Formula, that I can work to solve for "Sa":
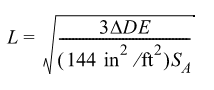
It then shows a "simplified" formula for this same calculation that can NOT be reverse engineered because it assumes a reasonable "stress allowed" number to approximate the short leg that is good for carbon steel and copper piping.
Short Formula:
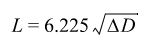
However, when we jump to the Z-bend section, ASHRAE only shows the simplified formula... I want the long-form equation for a Z-bend that I can reverse and solve for the stress.
Anyone happen to have a resource that shows the full long-form version of the Z bend formula?